8.3 Various Processes Used to Make Biodiesel
Some of the processes used in making biodiesel are different from what we’ve discussed. The first of these processes we’ll discuss is solvent extraction.
In the process of making biodiesel through transesterification, we noted that biodiesel and glycerol are the products, with some water formation and unwanted potential soap formation. So, the products are liquid, but they are also immiscible (do not dissolve in each other) and have differences in specific gravity. The specific gravity of the products is shown in the table below.
Material | Specific gravity (g/cm3) |
---|---|
Glycerol (pure) | 1.26 |
Glycerol (crude) | 1.05 |
Biodiesel | 0.88 |
Methanol | 0.79 |
In batch processing, gravity separation is used, and the products remain in the reactor; the reactor then becomes a settler or decanter. Once the reaction is finished, the product mixture then sits without agitation. After 4-8 hours, the glycerol layer settles at the bottom (because it has higher gravity) and the biodiesel settles at the top. However, if a continuous flow facility is utilized, the products separate too slowly in a settler, so a centrifuge is used. A centrifuge will spin the liquids at a very high speed, which helps to promote density separation. The figure below shows a few different types of industrial centrifuges that can be used for biodiesel separation.
One of the issues that can happen during separation is the forming of a layer containing water and soap, in between the glycerol and biodiesel. That will hinder the separation. Another issue is that glycerol contains 90% of the catalyst and 70% of the excess methanol. In other words, the glycerol fraction is kind of the “trashcan” layer of the process. The biodiesel layer also contains some contaminants, including soap, residual methanol, free glycerol, and residual catalyst. The catalyst in biodiesel is extremely problematic if introduced into fuel systems. One way to improve the separation is through water washing with hot water, as the contaminants are soluble in water, but the biodiesel is not. Water washing will remove contaminants such as soap, residual methanol, free glycerol, and catalysts. The water should be softened (had ions removed) and be hot (both the biodiesel and water should be at 60°C). Thorough mixing with the wash water is needed so that all the contaminants can be removed, but the mixing intensity should also be controlled so that emulsions do not form between the biodiesel and water. Sometimes acid is added in the wash process to separate out the soaps. However, the last portion of washing needs to be acid-free, so a step may need to be added to neutralize the glycerol.
There is more than one way to implement the washing process. For batch processes, two of the methods are: a) top spray and b) air bubbling (see figure below). For the top spray, a fine mist of water is sprayed top-down in a fine mist. The water droplets contact the biodiesel as the water flows down, separating out the impurities. Air bubbling is a method that uses air as a mobile phase. Air bubbles through a layer of water and carries water with it on the way up. As the air bubbles burst on the way up, water droplets are released and drop down on the biodiesel at the bottom, contacting the biodiesel and washing out impurities. It can be a relatively slow process; a combination of the two is also possible.
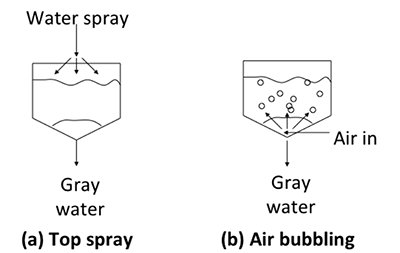
For continuous-flow processes, different equipment is used, which typically incorporates some sort of counter-current flow process. The lighter biodiesel is introduced at the bottom and the heavier water is introduced at the top, and as they flow the fluids contact each other so that the biodiesel at the top has impurities removed and the water flowing down out the bottom contains the contaminants. The figure below shows two types of counter-current units: a) counter-flow washing system and b) rotating disc extractor. Both units contain materials to increase the interaction between water and biodiesel. For the counter-flow system, packing increases the interaction, while for the rotating disk extractor, disks rotate around as the fluid flows through. These types of equipment are typically used on an industrial scale and need precise mechanical design and process control; these units cost much more than the other type of system.
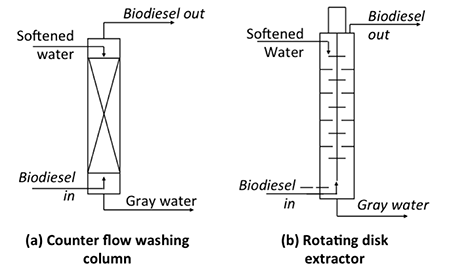
The most problematic step in biodiesel production, however, is water washing. It requires heated, softened water, some method of wastewater treatment, and water/methanol separation. Methanol recovery from water is somewhat costly using methanol-water rectification. Water can also be removed by vacuum drying. One of the alternative methods for removing water is the use of absorbent materials such as magnesium silicate. One company that provides a process for doing this is Magnesol, which is produced by the Dallas Group. Once the magnesium silicate removes the water, it can be regenerated by heating it up and evaporating the water. Methanol must also be removed from the biodiesel; one method for doing this is flash vaporization of methanol.
So, which type of process should be used? Should it be a batch or continuous flow system? Smaller plants are typically batch (< 1 million gallons/yr). They do not require continuous operation 24 hours per day 7 days a week. The batch system provides better flexibility and the process can be tuned based on particular feedstocks. However, in a commercial, industrial setting, most likely a continuous flow system will be used because of increased production and high-volume separation systems, which will increase the throughput. There are automation and process controls, but this also means higher capital costs and the use of trained personnel. It is feasible to have hybrid systems as well.
The primary byproduct is glycerin (aka glycerine, glycerol). It is a polyhydric alcohol, which is sometimes called a triol. It is a colorless and odorless liquid, which is viscous (thick-flowing) and sweet-tasting. It is non-toxic and water-soluble. Parameters to test quality are purity, color, and odor. Glycerol properties and chemical information are shown in the table below.
Chemical name | Propane-1,2,3-triol |
---|---|
Chemical formula | C3H5(OH)3 |
Molecular Weight, g/mol | 92.09 |
Density, g/cm³ @ 20°C | 1.261 |
Viscosity, mPa.s, @ 20°C (93% w/ water) |
1500 (400) |
Melting point, °C (°F) | 17.9 (64.2) |
Boiling point, °C (°F) | 290 – 297 (554-567) |
Auto-ignition, °C (°F) | 370(700) |
Flash Point, °C (°F) | 188 - 199 (370 - 290) |
Food energy, kJ/g | 18 |
There are several different applications that glycerol can be used for, including the manufacture of drugs, oral care, personal care, tobacco, and polymers. Medical and pharmaceutical preparations use glycerol as a means to improve smoothness, lubrication, and moisturize – it is used in cough syrups, expectorants, laxatives, and elixirs. It can also be substituted for alcohol, as a solvent that will create a therapeutic herbal extraction.
Glycerol can be used in many personal care items; it serves as an emollient, moisturizer, solvent, and lubricant – it is used in toothpaste, mouthwashes, skin care products, shaving cream, hair care products, and soaps. Glycerol competes with sorbitol as an additive; glycerol has a better taste and a higher solubility.
Since it can be used in medical and personal care products, glycerol can also be used in foods and beverages. It can be used as a solvent, moisturizer, and sweetener. It can be used as a solvent for flavors (vanilla) and food coloring. It is a softening agent for candy and cakes. It can be used as part of the casings for meats and cheeses. It is also used in the manufacture of shortening and margarine, filler for low-fat food, and thickening agents in liqueurs.
Glycerol is also used to make a variety of polymers, particularly polyether polyols. Polymers include flexible foams and rigid foams, alkyl resins (plastics) and cellophane, surface coatings, and paints, and as a softener and plasticizer.
Unfortunately, there is already enough glycerol produced for the glycerol market. Glycerol consumption in traditional uses is 450 million lb/yr, and traditional capacity is 557 million lb/yr. If we produce glycerol from making biodiesel, it has the potential to produce 1900 million lb/yr. Therefore, we need to find a new market for glycerol, or it will be wasted in some fashion.
There is research being done to find new uses for glycerol. This includes use in additional polymers as an intermediate, conversion to propylene glycol for antifreeze, production of hydrogen via gasification, as a boiler fuel (have to remove alkali), in an anaerobic digester supplement, and for algal fermentation to produce Omega-3 polyunsaturated fatty acids.