Compressor Stations
Video: How a Compressor Station Works (3:59)
Natural Gas Compressor Stations
Natural gas pressure at the wellhead may be sufficient to "push" the gas into a pipeline, but over time the gas pressure drops in the reservoir and the gas pressure will need to be boosted to get it to the pipeline and the marketplace. Once gas is in a pipeline, which may operate at a pressure of 1,500 pounds per square inch (PSI) or higher, its pressure may drop off due to frictional losses or drawing gas from the line. A natural gas compressor station like we're at here today is a transmission relay station. We have thousands of miles of gas transmission pipeline in the Northeast. As the customers take gas off the pipeline system, the pressure is reduced. So we have to add the transmission relay compressor stations to boost the pressure in the pipeline. It comes in through a suction line into the compressor station. It goes through a filter separator element that we have that takes out any impurities that might be in the gas. The compressor basically is driven by an engine, in this case, a turbine. The gas goes into the compressor, it boosts the pressure when it's in the compressor, it goes back out into a discharge line from the station, and it goes back into the main pipeline on a downstream side at a higher pressure.
What about Emissions?
We've gone to a primary utilization of solar turbine. Solar Turbines, from our standpoint, are state-of-the-art equipment. They have what they call a low emissions package that Dominion buys from them. It's a gas-fired turbine engine that drives the compressor. And by process of burning the natural gas to create the power to turn the compressor, the actual exhaust goes through an oxidation catalyst, which further reduces the emissions, to the effect when if you're standing at a natural gas compressor station and you're looking at the exhaust, you see no emissions. There are no emissions visible at a natural gas compressor station. The facility is operating at 100% capacity while we're standing here talking. As you can see, I'm talking in a normal tone of voice. I'm not having to raise my voice. The building is insulated. The exhaust itself is also covered with an insulation that basically mitigates the amount of noise coming from it. The amount of noise that's at a compressor station, outside the fence of a compressor station, is really very similar to what you would have if you if you're in your residential plan, standing in your front large yard, and a car goes by. I mean that's essentially the noise level that you're going to be hearing.
Is it Safe?
Here at Dominion safety is our primary core value. Everything we do is focused on safety. The facilities are monitored on a 24/7 basis by our gas control operations in West Virginia. We have people on site every day monitoring the facilities, checking to make sure everything is working within the right parameters. We do a lot of inspections to ensure that all the controls are in place and functioning properly. We have what we call an emergency shutdown system at our compressor stations. And what that does is it basically can shut the main valves coming in and out of the station such that the entire station can be isolated from the pipeline. From our perspective, the safety of our employees is paramount. We want them to be able to come to work every day safe and go home every day safe, not only that just themselves but their friends and family that live with them in the community as well.
The operation of a compressor station is really contingent upon the customer requirements at any given time. Typically in the winter, there's a lot of natural gas required for the heating load. So the natural gas compressor stations operate fairly frequently during the winter operations. During the summer, now with the advent of natural gas-fired power plants, have a fairly significant cooling load required in the summer. So we also run the facilities at some higher frequency in the summer than we would in the fall or the spring.
Components of a Compressor Station
Natural gas enters a compressor station through station yard piping and is passed through scrubbers and filters to extract any liquids and remove solids or other particulate matter that may be in the gas stream (see compression station yard diagram). Once the natural gas stream has been cleaned, it is directed through additional yard piping to individual compressors. Computers regulate the flow and number of units that are needed to handle the scheduled system flow requirements. Most compressor units operate in parallel, with the individual compressor units providing the needed additional pressure, before directing the gas back into the pipeline with full operational pressure restored. When the required boost in pressure is very high, several compressor units may be operated in stages (serially) to achieve the desired pressure in stages.
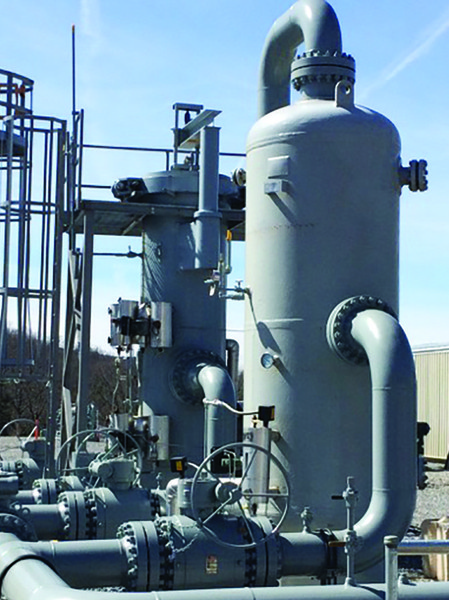
Compressor stations are an integral part of the natural gas pipeline network that move natural gas from individual producing well sites to end users. As the natural gas moves through a pipeline, distance, friction, and elevation differences slow the movement of the gas and reduce pressure. Compressor stations are placed strategically within the gathering and transportation pipeline network to help maintain the pressure and flow of gas to market.
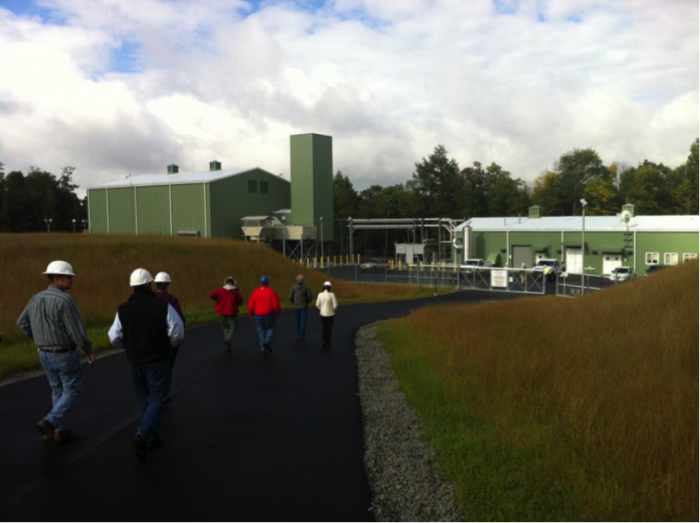
As natural gas is compressed, heat is generated and must be dissipated to cool the gas stream before leaving the compressor facility. For every 100 psi increase in pressure, the temperature of the gas stream increases by 7–8 degrees. Most compressor stations have an aerial cooler system to dissipate excess heat (an “after” cooler). The heat generated by the operation of the individual compressor units is dissipated via a sealed coolant system similar to an automotive radiator.
In wet gas areas, or areas that produce natural gas liquids (NGLs), changes in pressure and temperature cause some of the liquids to drop out. The liquids that drop out are captured in tanks and trucked off-site. The liquids captured are called natural gasoline or drip gas, which is often used as a blend in motor gasoline.
Most compressor stations are fueled by a portion of the natural gas flowing through the station, although in some areas of the country, all or some of the units may be electrically powered primarily for environmental or security reasons. Gas-powered compressors may be driven by either conventional piston engines or natural gas turbine units. There are site design and operational differences, as well as unique air and sound emissions, between these competing compressor engine technologies.
There may be one or more individual compressor units at a station, which can be out in the open, or more often, housed in a building to facilitate maintenance and sound management. Newer units are often housed one per building, but there may be multiple units in one large building. Compressor buildings generally incorporate insulated walls, shielded exhaust systems, and advanced fan technology to dampen sound. Newly constructed compressor buildings may incorporate these features where local, state, or federal regulations require noise mitigation.
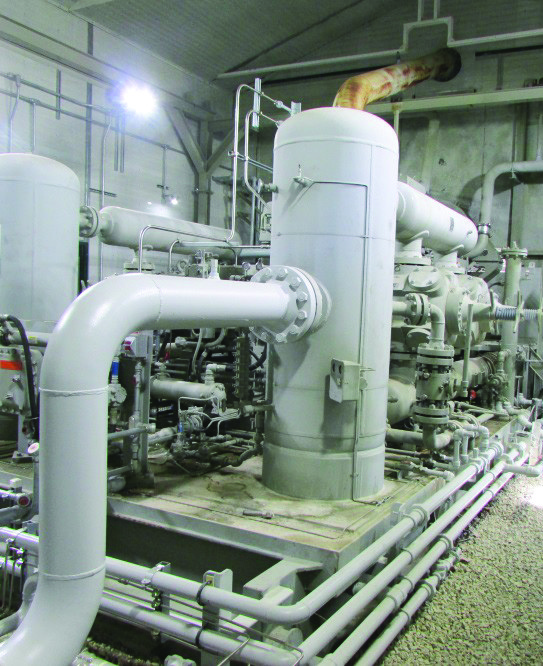
Compressor station yards for gathering lines are often larger than transmission line compressors due to multiple pipelines coming into the complex, and sometimes, additional equipment needed to filter and remove liquids from the gas stream (see compression station yard diagram below). Other components of a compressor complex include backup generators, gas metering equipment, gas filtration systems, and system monitoring and safety controls. There may also be odorization equipment to add mercaptan, which provides the distinctive sulfurous odor to natural gas for safety and leak detection purposes.
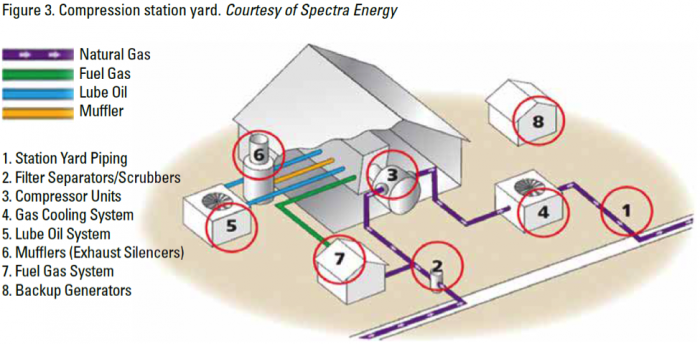
- Station Yard Piping
- Natural Gas pipe connecting to 4
- Filter Separators/Scrubbers
- Natural Gas pipe connected to 7 & 3
- Compressor Units
- Natural Gas pipe extending to 7, 4, and 2.
- Gas Colling System
- Natural Gas pipe connected to 1 & 3
- Lube Oil System
- Lube oil - 2 pipes
- Mufflers (Exhaust Silencers)
- Muffler
- Fuel Gas System
- Fuel Gas pipe
- Backup Generators
Please refer to Penn State Extension Publication ‘Understanding Natural Gas Compressor Stations’ to learn more about the types of compressor stations, regulatory oversight, safety, and landowner and community considerations.
Required Reading
Check Your Understanding
Why are compressor stations an integral part of the natural gas pipeline network? Consider how you would answer this question and then check your answer below.
Compressor stations are an integral part of the natural gas pipeline network that moves natural gas from individual producing well sites to end users. As the natural gas moves through a pipeline, distance, friction, and elevation differences slow the movement of the gas and reduce pressure. Compressor stations are placed strategically within the gathering and transportation pipeline network to help maintain the pressure and flow of gas to market.