
Hydrotreatment Processes
Process objectives, conditions, and configurations are similar for all hydrotreatment processes [1]. As an example, HDS list, below, lists the project objectives and selected conditions for HDS processes. Minimization of cracking (or any other chemical change that is not needed for removing heteroatoms) and minimization of hydrogen consumption are the two principal objectives of hydrotreatment processes for reducing the heteroatom concentrations to the desired levels in the reaction products. These objectives are achieved by careful selection of process conditions that need to be adjusted based on the chemical composition of the feedstock. You can see in HDS list, that more severe reaction conditions (e.g., higher reaction temperatures, higher hydrogen/feed ratios, and lower space velocities) are necessary for treating heavy residue compared to treating light distillates. Catalysts have shorter lives in residue treatment processes, as well, because of harsh reaction conditions and more excessive deposition on catalysts during the treatment of heavy residue.
HDS (Hydrodesulfurization)
Objectives
- minimizing cracking
- minimizing hydrogen consumption
Process Conditions |
Light Distillate |
Heavy Residue |
Temperature,&;ºC |
300-400 |
340-425 |
LHSV, h-1 | 2-10 | 0.2-1 |
H2/Oil, scf/bbl | 300-2000 | 2000-10000 |
Catalyst life, years | 10 | ~1 |
Note: LHSV (Liquid Hourly Space Velocity) – the volumetric flow rate of liquid reactant passing through a reactor divided by the volume of the catalyst in the reactor, measured in units of h-1. Lower LHSV (i.e., longer exposure to catalyst in the reactor) is needed for more challenging hydrotreatment tasks.
Figure 9.9 shows a process flow diagram for HDS. The feed is introduced into a fixed-bed catalytic reactor along with hydrogen, and the products are sent to a high-pressure separator to separate H2 and H2S gases from the hydrocarbons. The gases are sent to a scrubber with a basic solution (containing ethanol amine or diethanol amine) to remove H2S that is sent to the sulfur recovery unit and H2 is recycled to the treatment reactor. Desulfurized products are sent to a fractionator to separate C3 and C4 alkanes (LPG) and the liquid products.
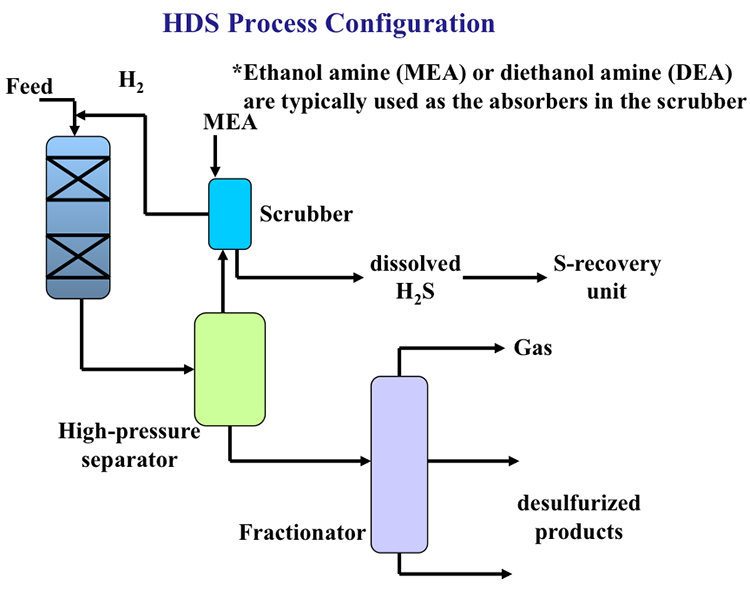
For HDS, HDN and HDM sequential reactors can be configured with different catalysts optimized for the targeted heteroatom removal. Figure 9.10 shows staging of the HDM and HDS operations. The first step in a series of reactors is always HDM because of the unique removal mechanism of the metals (Ni and V), as solid materials on catalyst surfaces, catalysts with large pores in the support materials are needed so that the problems with reactor plugging can be avoided. Following the removal of metals, HDS and HDN can be conducted on medium-pore and small-pore catalysts, in some cases simultaneously in the same reactor or the same catalyst bed.
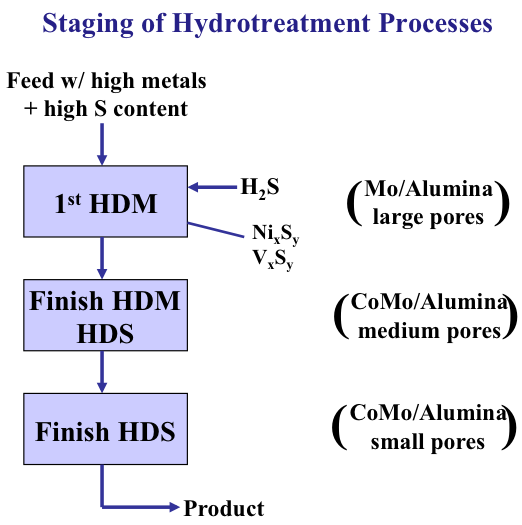
Staging of Hydrotreatment Processes
-Feed w/high metals + high S content
-First HDM
-H2S, NixSy, VxSy
-Mo/Alumina, large pores
-Finish HDM then HDS
-CoMo/Alumina, medium pores
-Finish HDS
-CoMo/Alumina, small pores
-Product
Increasing sulfur contents of the crude oils available for the U.S. refineries on one hand, and decreasing sulfur contents of regulated fuels on the other, have increased the sulfur production in the U.S. refineries as a by-product to 40,000 tons/day [4]. This is sufficient capacity to meet all sulfur demand for the chemical industry, particularly for H2SO4 production used in many chemical industries. One should note that this quantity of sulfur comes only from desulfurization of the fuels that are subject to sulfur regulation. A significant fraction of sulfur in crude oil (>60%) is concentrated in the heavy ends (e.g., residual fuel oil, asphalt) that are not regulated for sulfur content.
[1] Petroleum Refining, by J. H. Gary, G. E. Handwerk, M. J. Kaiser, 5th Edition, CRC Press NY, 2007, Chapter 9, Hydrotreatment, pp. 195-203.
[4] Petroleum Refining, by J. H. Gary, G. E. Handwerk, M. J. Kaiser, 5th Edition, CRC Press NY, 2007, Chapter 12, Product Blending, pp.257-270.