
Uses of Hydrocracking
In a refinery, hydrocracking complements catalytic cracking by taking on the more aromatic feedstocks that resist cracking, including the byproducts of FCC, such as light cycle oil (LCO). Hydrocracking can also be used to upgrade residual fractions using different reactor configurations and catalysts depending on the complexity of the upgrading tasks, as shown in Figure 7.12. As shown in Figure 7.13, for hydrocracking a relatively light feedstock (e.g., atmospheric residue), a fixed-bed configuration and relatively large-size catalyst particles can be used. In extreme cases with very heavy vacuum residue, an expanded bed configuration is used, in which very fine catalyst particles are entrained in the feed at high hydrogen pressures (high hydrogen/oil ratio). These extreme reaction conditions are necessary to prevent extensive coking on catalysts that could shut down the process. For intermediate cases, an ebullated (fluidized) bed configuration can be used, as shown in Figure 7.13.
In the United States, hydrocracking of LCO (from FCC) provides a large proportion of the diesel fuel production because straight-run LGO is a preferred stock for FCC to produce gasoline as the principal product. The major licensors of hydrocracking processes include Chevron, UOP, ExxonMobil Research and Engineering, BP, Shell, and BASF-IFP.
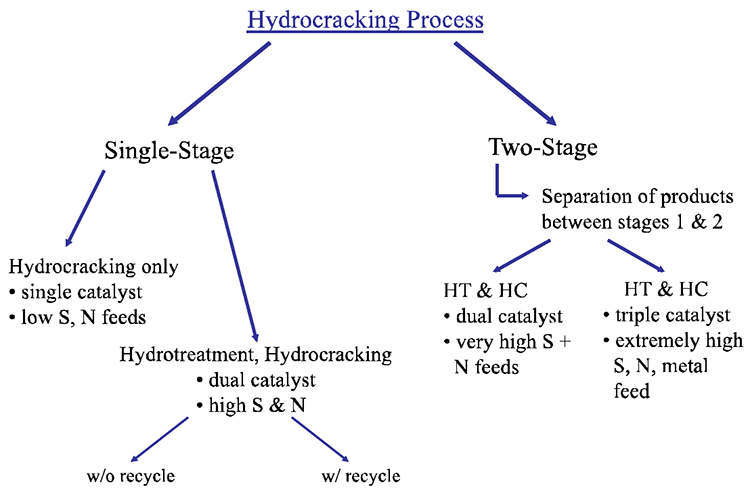
Hydrocracking Process
-Single Stage
-Hydrocracking only
-single catalyst
-low S, N feeds
-Hydrotreatment, Hydrocracking
-dual catalyst
-high S&N
-can be done with or without recycling
-Two-Stage (separation of the products between stages 1 & 2)
-HT & HC
-dual catalyst
-very high S + N feeds
-HT & HC
-triple catalyst
-extremely high S, N, metal feed
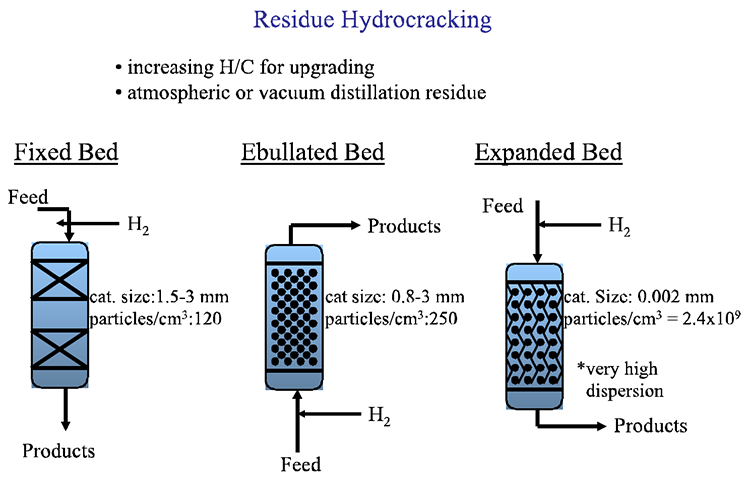
Residue Hydrocracking
-increasing H/C for upgrading
-atmospheric or vacuum distillation reside
Bed Type | Cat. Size | Particles/cm3 |
---|---|---|
Fixed | 1.5 - 3mm | 120 |
Ebullated | 0.8 - 3mm | 250 |
Expanded | 0.002mm | 2.4x109 |
Hydrocracking vs. Catalytic Cracking
Catalytic Cracking - FCC | Hydrocracking |
---|---|
-carbon rejection -endothermic -acid catalyst -more gas -more coke |
-hydrogen addition -exothermic -metal catalyst on acid support -less gas -less coke -costly process ($$$) |
- Hydrocracking involves C-C bond cleavage to produce lighter HC's
- More liquid yield with HYDRCRC
- More hydrogenated products
- Cracking is less severe
- Secondary cracking reactions are minimized by stabilization of active species by hydrogen
- Hydrocracking is more flexible w.r.t. the feedstock
- Refractory feedstocks (i.e. aromatics) can be processed
- C-C bond breaking after saturation with hydrogen
Above, we compare catalytic cracking (FCC - a carbon rejection process) with hydrocracking (HYDRCRC) with respect to the major attributes of both projects. Clearly, in a flexible refinery with a wide range of crude oil feedstocks, both processes are needed for the optimum conversion of the crude oil into desirable refinery products.