
Lesson 3.1: General Concepts of Exploration
You’ll recall the goals of exploration from Lesson 2.1 of Module 2. From a successful prospecting effort, we believe that we have found an economic concentration of a mineral. In the exploration stage, we will want to define this deposit in as much detail as practicable. We want to know its shape, its size, its orientation, its depth below the surface, the grade and perhaps chemical composition of the ore, and several geotechnical parameters for the deposit and the surrounding rock. That’s a lot of information, and the acquisition of information is rarely cheap! Hence, the previous discussion about managing risks. One of the sure ways of increasing the certainty about the characteristics of the deposit is sampling. We can use a variety of techniques to estimate the characteristics of the deposit, including geophysical imaging and structural geology. Above all, data obtained from samples can be definitive, and generally the more samples that we can take, the better.
For near-surface deposits, we may use trench samples, which literally entails digging a ditch, and then observing and sampling the exposed material. Similarly, we could take pit samples where we dig a larger hole. And there are other methods. The most commonly used technique for shallow and deep deposits is drilling. There are two types of exploration drills in service: one that produces cores and the other that produces chips or cuttings. Both drill holes of a relatively small diameter of approximately 1.5” to 4”. The difference in the “product” from these drills is illustrated in Figure 3.1.1.
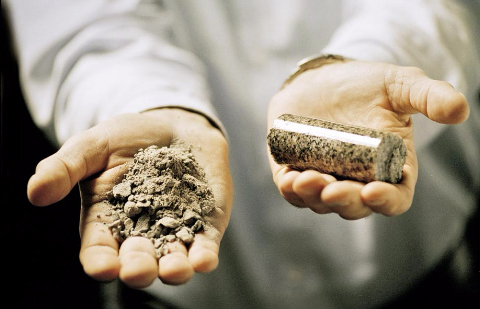
The core is obtained with a drill that has an outer barrel with diamond cutting bits. As the drilling progresses the rock core is undamaged and provides a detailed record of the rock layers. Information on structural features such as joints is preserved. Normally, a field geologist is conducting or supervising the core drilling and will keep detailed records or “logs” of the cores as they are collected and carefully placed into core boxes.
Photos of a drill and associated components are found on Atlas Copco's Conventional Core Drilling page. Take a look at the core bits, core barrels, and drilling rods. You can see a few examples of core boxes and the cores being placed into them.
In contrast to core drilling, chips are obtained with a traditional rotary-percussion drill bit, in which the bits are the same diameter as the hole. The cuttings are collected in a tube inside of the drill rod. This process and the drills are often known as reverse circulation. Cuttings provide information on the type of material and its composition, but structural information is lost. Coring cost per length of the hole is several times more than for cuttings. Both are valuable as we endeavor to define the deposit at a justifiable cost. The difference in the bits that produce the chips versus cores is evident in this picture (Figure 3.1.2).
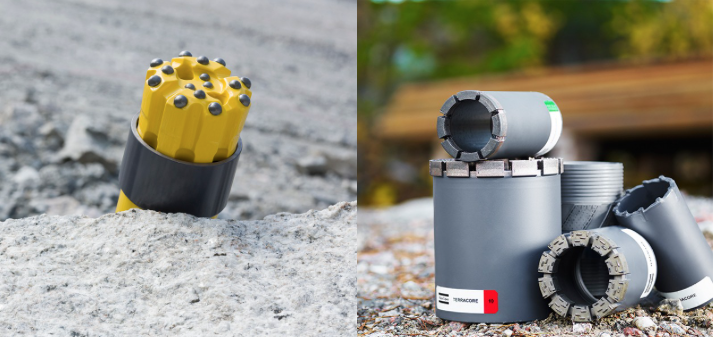
Characteristics of a typical drill rig for surface application are found in this brochure: Atlas Copco Surface Exploration Drill. Later we’ll talk briefly about conducting an exploration program during underground mining. Doing so requires a different configuration of the drill rig, due to the more confined space of the underground mine. Pictures and characteristics of a rig for use in an underground mine are found in this brochure: Atlas Copco UG Exploration Drill
Regardless of which type of drill is used to sample the deposit, it is important to develop a sampling plan, i.e., how many holes will be drilled, and where will these holes be drilled? Will they be spaced uniformly on a grid for example, or perhaps located at irregular intervals? What is the maximum spacing between holes? Practical limitations may limit where we can place our holes. We may not have the surface rights at some points on the pattern, which means we can’t drill from that location. Or other points may be inaccessible due to rugged terrain, the absence of roads to access the area, or maybe there is a shopping mall at the location where we would like to place a hole. Thus, our drilling program may have fewer holes than we’d like due to cost consideration, and the holes may not be placed exactly where we’d prefer to locate them. These are considerations that will keep you awake at night! Why?
Simply put, if we do not take a sufficient number of samples, and we have:
- a large deposit of irregular shape, it is possible that we can completely miss parts of it and grossly underestimate the size of the deposit,
- a small deposit of irregular shape, it is possible that most of our holes will intersect the deposit, leading us to conclude incorrectly that the deposit is massive in size,
- a deposit with a grade or other chemical characteristic that is highly variable, it is possible that we will grossly under or overestimate the value of the deposit.
These are not abstractions! There are real-world examples where these events have transpired, and with very bad consequences for the company. So, how do we know how to locate our drill holes to reduce the likelihood of reaching incorrect conclusions about the deposit? First, knowledge of the geology associated with the target mineral is useful. If we are exploring a coal deposit in western Pennsylvania, we know that it will be a relatively flat lying and tabular deposit. On the other hand, if we’re exploring a gold deposit in Nevada, we can consider that the orebody is likely to consist of veins of varying thickness. Clearly, this geologic knowledge, and the help of a geologist will help us to design an effective sampling program.
There are a few guidelines that have developed over the years.
- A regularly spaced pattern will generally yield more information at a reduced cost.
- The maximum spacing of the holes should be less than the minimum dimension of a deposit that would be mineable with a given mining method.
- Non-vertical holes may be better for steeply dipping veins or lenses. (see Figure 3.6 of the text)
- Data from widely spaced patterns can be evaluated, and then additional holes can be added as appropriate. (see Figure 3.7 of the text)
- Experience gained from other exploration programs is useful. For example,
- A Bureau of Mines study found that holes placed on 1200’ centers would yield sufficient information on the Pittsburgh coal seam
- Patterns for bituminous coal deposits, in general, range from 500’ x 500’ to 3000’ x 3000’
- Typical patterns for porphyry copper deposits are 150’ x 250’ to 200’ x 400’
- Typical patterns for taconite deposits are 100’ x 200’ to 200’ x 300’
It is important that our spacing be such that we can ensure geologic and grade continuity of the ore between holes.
The number of holes and the drilling pattern will help us to accurately estimate the size, shape, and attitude of the orebody, and this is critical. In most cases, we are equally concerned with the grade of the ore or perhaps some other characteristic. Suppose that we’ve done a calculation and we know that the minimum grade at which we can make a profit is 5%, i.e., for each ton of ore, we have 100 lbs. of the mineral of interest; and further, suppose that the grade found in the drill holes ranges from 3% to 7%. Will it be profitable to mine this deposit? Or we may be looking at the CaCO3 content of the limestone, and there will be a minimum concentration that is acceptable for our market. Sometimes it is an impurity in the deposit, which is of greater concern. For example, if the impurities in our salt deposit exceed 2%, we will be unable to sell our product into the more lucrative market for chemical-grade salt, and instead will have to sell it for deicing of roads. In each of these three examples, the value of the deposit will be estimated by analyzing the samples obtained from the drilling program.
Let’s think about this for a case in which the holes are spaced on a regular grid of 1000’, and the diameter of the drill holes is 3”. Suppose we analyze the core for a grade. Think about this: based on a sample of less than 0.1 ft2, we will estimate the grade of the ore over an area of 1,000,000 ft2. This may seem crazy, but if we have prior knowledge about the typical variability of a characteristic in a certain type of deposit, and we have chosen our hole spacing based on that knowledge, then we can be reasonably confident in the estimate.
Fortunately, it is unlikely that you will have to design a sampling program, on your own, in the early years of your career. Nonetheless, you should understand the goals and challenges of the exploration program.
Important outcomes from the exploration program are estimates on the size and value of the deposit. Some of you may have heard terms like "proven" and "probable" or "inferred" to describe the resource or the reserve. These words have a specific meaning and are not to be confused. Not only is this important so that we can understand each other when we talk, but the terms have legal significance so that someone who is considering investing in your mining project is not misled, or worse, deceived. Let’s look at the definitions, and then this will become even more clear.
Resource: a mineral resource is a concentration of naturally occurring solid, liquid, or gaseous material in or on the earth’s crust, in such form and amount that economic extraction of the commodity is potentially feasible.
Resources are further categorized based on the certainty of our estimates.
Measured Mineral Resource: that part of the resource for which tonnage, mineral content, grade, and physical characteristics can be estimated with a high level of confidence. The data must be based on detailed and reliable physical evidence, e.g., drill holes, trenches, outcrops, etc., and sample locations must be spaced sufficiently close to confirm geologic and grade continuity.
Indicated Mineral Resource: similar to a measured mineral resource, but with a reasonable, not a high-level of confidence. Typically, this is because the spacing of the physical samples, e.g., boreholes, is too widely spaced to confirm continuity, but close enough to reasonably assume continuity.
Inferred Mineral Resource: that part of the resource for which tonnage, mineral content, grade, and physical characteristics are known with a low level of confidence because the estimate is inferred from geologic evidence that has not been verified with physical data, e.g., boreholes.
While the mineral resource is an important parameter to determine, investors and mining companies gain little benefit from minerals in the ground. They become valuable if they can be mined. This distinction is accounted for in the definition of a reserve.
Reserve: a mineral reserve is that portion of the mineral resource that can be mined economically at a point in time.
Reserves are further categorized as follows:
Proved Mineral Reserve: that part of a measured mineral resource that can be economically mined at a point in time.
Probable Mineral Reserve: that part of an indicated mineral resource that can be economically mined at a point in time.
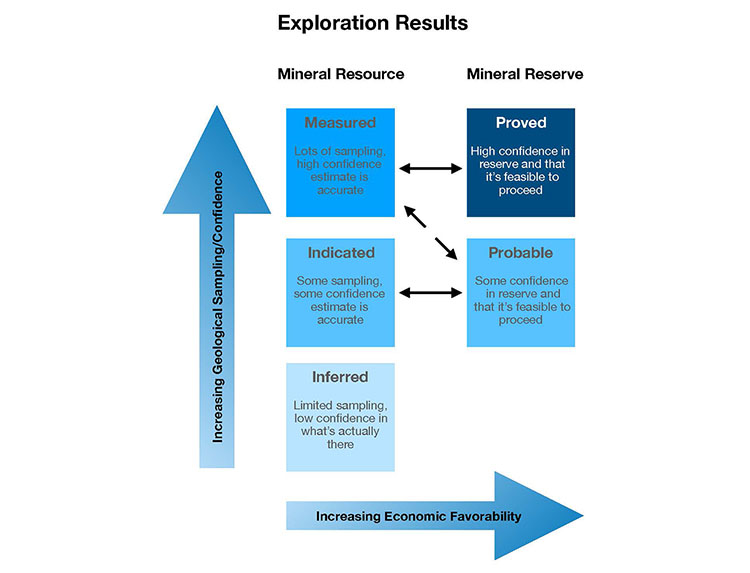
The real value in a potential mining project is in the proved mineral reserve, rather than the probable part of the reserve. The distinction between these two is the degree of certainty in the resource estimate. This further underscores the importance of designing a sampling program and assembling a team of geologists to ensure and confirm geologic and grade continuity.
We have talked about using:
- the drill hole information to define the spatial characteristics of the deposit;
- cores to determine geotechnical features of the orebody and the surrounding rock; and
- cores and cuttings to establish grade and chemical composition, among others, by analyzing the samples in the lab.
I did not mention it earlier, but we will normally conduct metallurgical or process testing on the core or cutting samples too. This information is used to establish certain market qualities of the ore, and to better understand the mineral processing that will be required to beneficiate the ore.
It should also be noted that we can lower instruments down the drill holes, assuming the holes are of sufficient diameter, to “log” the holes. The logging may be done visually using a camera, or with geophysical instruments including gamma-ray and acoustic devices. These logs help to better define the lithology and other characteristics.
A quality exploration program is essential to establish the feasibility of mining the resource, as well as to determine the value of the reserve. While the major exploration work is normally completed to support the feasibility study and subsequently the engineering design of the mine, exploration may continue throughout the life of the mine. In complex ore bodies, exploration drilling will continue in advance of mining throughout the mine’s life. Even in the case of fairly predictable deposits, e.g., a coal seam, conditions may be encountered that require exploratory drilling to define the size of a want area, i.e., an area where the coal has been displaced with a shale or a sandstone, for example. Other than learning a bit more about the methodology for reserve estimation, we are ready to move into the next module where we focus on the development stage.