
7.1.1: Mine Planning Details
Mine operators want to maximize profit while ensuring safe and environmentally responsible operations. There are many constraints that will limit the profitability of a mining project. Many of these constraints are not well known at a given point in time, and some of them can change unpredictably over time. These uncertainties create risk, and this creates complexities for mine operators. Major uncertainties for a mining project are grade, tonnage, and geotechnical conditions, as well as economic-related uncertainties such as fluctuations in price and demand for the mined product.
Good mine planning throughout the life of the mine is an essential prerequisite to realizing the financial goals of the project. Moreover, it is very important for you to appreciate the time value of money. Simply put, the value of $1 today is much higher than the value of $1 that will be received in the future. We use a metric known as the net present value, which allows us to compare future revenues or costs at the same point in time. Suppose, for example, that your project will produce $100 of revenue this year, $500 in year 5, and $1000 in year 10. My project will produce $600 this year, $600 in year 5 and $100 in year 10. Let’s say that each project requires you to make the same investment today, to realize these revenue streams. For this illustration, the amount of your investment is immaterial, but it is the same for both of them. Which project is the better investment? On the face of it, your project appears to be the better investment. Over ten years, it will return $1600, whereas my project will return only $1200.
However, this comparison neglects the time value of money. If I have money in hand, I can put it in the bank and earn interest, for example. Let’s suppose that the interest rate is 10%. Then, the question becomes what amount of money would I have to invest today at 10% so that in 5 years it would equal $500. In other words, what is the present value that will accumulate to $500 if it earns 10% interest each year for 5 years? The answer is $310. In other words, that future earning of $500 is only worth $310 today. What about the $1000 that you expect to earn in 10 years? It has a present value of $385. So, the present value of your project is ($90+$310+$385), or $850. The present value of my project is ($545+$372+$38), or $955. Thus, the value of my project is better than yours, based on the net present value. The interest rate that we use for this calculation is also known as the discount rate. As you can see, the present value of a dollar earned far in the future is very little. Further, who knows what the world will look like in 10, 20, or 30 years? So much can change. For these reasons, the decision to move forward with a project is influenced heavily by what happens in the first five or so years of operation. For now, do not worry about the calculation of present value, but only the concept of present value and how it influences mine planning and investment decisions.
In MNG 412, you will learn about several economic tools to evaluate the merits of a project, and net present value is only one. Payback period, discounted cash flow, internal rate of return, among a few others, will help to inform a decision on the worthiness of a given project. Regardless, without accurate mine planning, the investment calculations will be of little value!
As a general rule, if we are to maximize the project’s profitability, we need to maximize its net present value. Based on this concept, it makes sense that we plan our mining activity to recover the part of deposit that will yield the highest profits earliest in the life of the mine. Profit is determined by subtracting cost from income:
Profit = Income – Cost
In today's mining industry, it is the income or cash flow generated in the first 5 to 7 years of the mine life that will either make or break a surface mining operation, not the remote economics of the ultimate pit limit, which is usually at least 20 years away. Therefore, if we want to maximize profit, we have to define two objectives: (1) maximize the income and (2) minimize the cost.
How do we maximize income?
- by mining out the highest grade of material as early as we can
- by mining out as much material as we can sell at the earliest possible time
What are some of the ways to minimize the cost?
- minimizing waste removal operation
- minimizing the cost of the unit and auxiliary operations
A question that may rise in your mind is: Why don’t we use a couple of huge pieces of equipment to extract all of the ore during the first year, instead of spending say 15-20 years in one operation? Actually, that is a good question at this point. Here are some reasons why that strategy isn’t practical.
Insufficient Market Demand
It is unlikely that we would be able to sell all of the product in a short time. Therefore, we would incur expenses in the present year, but not receive income to offset those expenses until a future time. Given the time-value-of-money discussion that we’ve had, we certainly don’t want this. Moreover, when you have product to sell, but no buyer, you incur additional “penalties.” Namely, you are taking up space around your plant, or you are incurring a charge to “store” the material elsewhere; and the quality of your product may deteriorate as it lies around.
Increased Equipment Costs
The purchase price of equipment increases with size and can become disproportionately more expensive if the piece of equipment is not in a common market range. Therefore, a small fleet of very large equipment will cost us much more than a larger fleet of smaller equipment of common size with the same overall capacity. However, the unit operating cost, which is the sum of maintenance and operating expenses for a fleet of very large equipment can often be significantly lower than a large fleet of small equipment.
Years ago, mining companies believed that bigger equipment is always better. Their reasoning was that even though the ownership cost is greater for bigger equipment, the unit operating cost is lower. Therefore, the overall unit cost, which is the sum of the unit ownership and unit operating costs, of the bigger equipment will be lower. It was true, to some extent. However, if a single piece of large equipment breaks down for a couple of hours, it will significantly delay production. On the other hand, if we have a fleet of smaller pieces of equipment, even if one needs maintenance, the rest of the fleet can generally cover its absence. Moreover, the unit operating cost of bigger equipment, especially the maintenance cost, dramatically increases as the equipment ages. Consequently, the “bigger is better” strategy must be carefully analyzed.
Higher Mine Development Costs
If we want to use really big equipment, then we’ll have to change the design parameters of our mine. Larger equipment requires sufficient space to operate. For example, if we’re talking about a larger truck, the haul roads will need to be wider, and we’ll need a better road bed and bearing surface, i.e., a more expensive haul road that will remain stable under the heavier truck weight. Wider roads in a pit will necessitate a higher stripping ratio, since the pit walls will be pushed back to the waste area, and this will increase the mine development costs.
Consider this figure in which we have an orebody shown in blue and two different pit limits for two different roadway widths. The blue pit limit corresponds to a wider road than the orange pit limit. As you can see in the below figure, the blue pit needs additional waste removal equal to the dashed area, compared to the orange pit. Therefore, more waste is now mined out per ton of ore, and the stripping ratio will be higher.
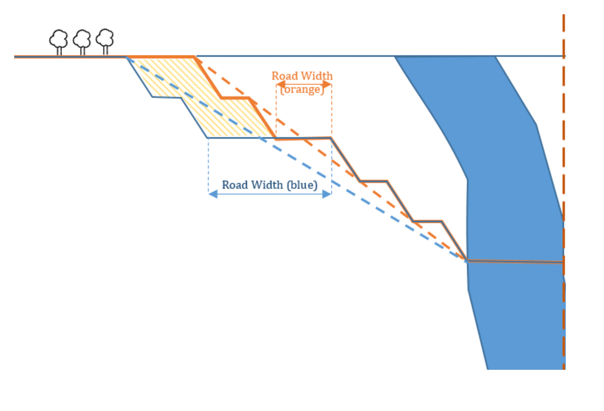
Loss of Selectivity
We talked earlier in the course about selectivity, and you will recall that selectivity is a measure of how effectively we can extract the ore of interest while taking as little waste material as possible. Larger mining trucks need to be matched with larger loading equipment; and larger loading machines have larger buckets. A large bucket reduces selectivity in loading, and that means you will dilute more of the ore with waste material than with a smaller piece of loading equipment.
This effect can be illustrated by considering the block of ore shown here, in Figure 7.1.3(a), assume that we have two options to load the material: a large bucket shown by the blue outline in Figure b and a small bucket the size of the blue outline in Figure c. With the large bucket, we will load all of the ore in the block, shown in orange, as well as the waste material shown in white. With the small bucket, we can be more selective, and taking three small bucket loads we get all of the ore with far less waste. As you can see, the option with the small bucket will reduce the dilution, and this in turn will reduce the unit cost of production.
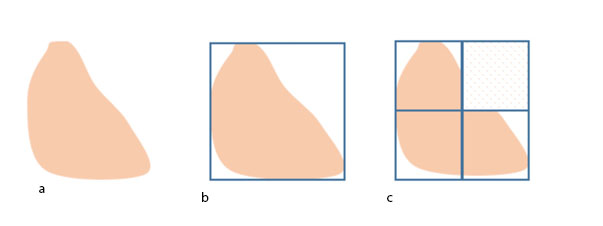
Equipment Life Cycle
The service life of mining equipment is measured in tons, hours, or years, depending on the type of equipment. A haul truck might have a life of 100,000 hours of operation, which may translate into 15 years of service life at a particular mine, and maybe as much as 20 years at a different mine with a different work schedule. Given the high capital cost of mining equipment, much effort is given to match the life of equipment with logical periods of production at the mine. This is yet another reason why mine planning is so important, to ensure that maximum benefit can be obtained from every piece of equipment over the life of the mine.
It is vital for a mining operation to determine an operationally viable mining sequence for the deposit and, subsequently, a production schedule that is achievable and economically sound. The Mine Planner's objective is to schedule and plan operations to achieve maximum return (of profit) on investment, through capital investment (e.g., mobile equipment), mine design, production scheduling, and preparation of the mineral product according to specifications that are required for the market. Therefore, “quantity” and “quality” would be important “drivers” in mine production planning.
BEFORE MOVING ON TO THE NEXT LESSON, please take a little time to think about the concepts presented in this section of this lesson. These will be underlying themes in many other topics.