
7.1.2: Mathieson's Planning Objectives
We’ve talked about the economic foundation of mine planning, and we’ve looked at several examples of how the mine design and the mine schedule can affect the economics. This is a good foundation for understanding the material in this course, as well as preparing you for more detailed studies in later courses. I want to conclude this lesson on mine planning by presenting a list of objectives to guide your mine planning decisions.
The starting point for your mine planning activities will be the geological model of your orebody; and this will be true, regardless of whether you have come into the planning process at the startup of the new mine, or after the mine has been in operation for years. You will have a block model, which details the grade of the ore in discrete categories and locations. The size of the blocks and the number of categories is a separate decision, but one that does not need to be addressed here. Consider this block model, which uses one of five grade ranges for each block. So, this is your starting point – where do you go from here? Undoubtedly, your approach will be multifaceted. There is a set of planning objectives first compiled by Mathieson and published in 1982. These objectives apply more or less to underground as well as surface mining, although his famous paper was directed at the surface mining community.
Here is a list of the major objectives of any surface mine planning exercise at the feasibility level:
Mining the “Next Best” ore
Mine orebody in such a way that for each year the production cost to produce a given amount of final product is minimized. What do we mean with the “Next Best”? The next best ore block here is the block that (i) maximizes the profit and (ii) does not contradict any other constraint or limitation, e.g., equipment operating room and slope design. To find the “next best” in the above figure, we will look for the red blocks that are close to the surface. We chase the red blocks because they contain a higher grade of ore that is easiest to mine. What do I mean by easiest to mine? I mean minimizing the production costs, and this normally suggests closest to the surface without any complicating factors. A complicating factor would be an environmental constraint or a geologic anomaly, for example.
Maintain sufficient ore exposure
Give yourself options on which mining face or faces will be scheduled for production on a given shift. If you normally have five active faces on any given shift, then you will want to have at least ten faces available for work on any given shift. Then, if there are unexpected ground control or other problems, you can simply move active work to a different face. Moreover, mining operations try to maintain enough ore exposure to meet production needs for an extended period, e.g., six months. This helps the company to reduce the risk that unforeseen events will adversely impact production. This is particularly true in the early years that are so critical to economic success. Unforeseen events could include a shortage in the equipment fleet due to delivery delays or significant breakdowns, labor issues due to union strikes, or difficulty in recruiting and retaining certain positions, adverse weather events, slope stability issues, and so on. Don’t forget to account for geological and engineering miscalculations. In the early stages of mine planning, geologic and operational information is limited, and this creates a greater level of uncertainty.
Maintain proper operational parameters
Adequate bench width and properly designed haul roads are essential to achieving the design level of production. Limited operating space on the bench can increase the cycle time of the operation, which will decrease productivity and production, and it may pose a safety hazard for the equipment and workers. Improperly designed haul roads can: increase the round-trip cycle time, which will affect productivity and production; greatly increase tire wear, and tire replacement represents a major cost element in many surface operations; and create safety hazards.
Let’s take a look at this picture of an open-pit copper mine. A loading and hauling operation is identified with arrow #1. If there were not enough operating room for the shovel, it would take longer for the shovel to dig, load, and dump the material. Concurrently, the truck driver will likely require more time to maneuver into position for loading. Arrow #2 points to a loaded truck traveling uphill to the dumping point and an empty truck making the return trip down-hill to the loading point. If proper operating room is not maintained, the trucks will need to reduce speed when passing. More importantly, there may be an increased risk for a truck to lose control and then go over the edge or crash into another truck. Therefore, it is incumbent on the mining engineer to design properly the benches and haul roads to ensure that safety and production are not compromised.
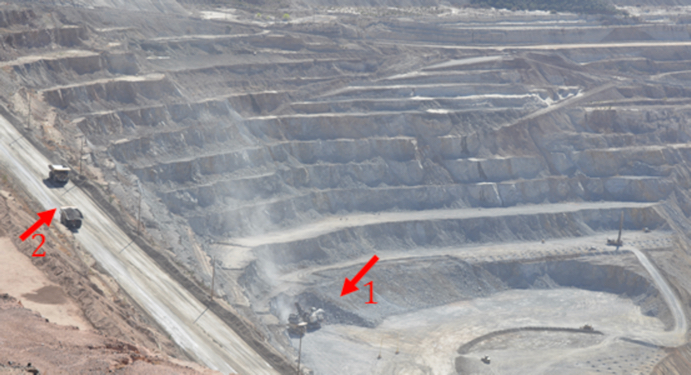
Defer stripping
As we discussed before, we would like to expedite profit making in the early years of operation, and to the extent that it is logical and achievable, we want to minimize the amount of stripping required to access the orebody. In the process of deferring stripping, we don’t want to compromise other objectives, such as the two that we just discussed.
Minimize the risk of delays in the initial cash flow
The production rate that is used for the early years of the mine is one of the more critical variables in determining the initial cash flow. Yet, it is also the variable that is subject to significant change over which you may have little control. Equipment delivery, outside contractor performance, workforce startup and training issues, and initial geologic uncertainty are examples of factors that can halve your production target in a given year. Imagine if your financial projections as supported by mine planning missed their target by 50%! Once again, you’d be looking for a new job! Consequently, the first year or two of production is de-rated to account for these uncertainties. If you were designing the mine to produce 6 million tons per year, it would not be unreasonable to choose a target for two million for the first year and three million for the second year. These aren’t arbitrarily chosen but will be based on simulations and risk analysis. The point here is that it is important to determine achievable production levels in the first few years of the mine life.
Maximize pit slope, while minimizing the risk of slope failure
We’ve looked at a few examples to illustrate the effect of the ultimate pit slope on stripping ratios and economics; and the “take-away message” is that the steeper the slope, the more favorable the economics! Unless, of course, you have slope failure! And then, once again, you are looking for a new job! Just kidding ... Even with very good ground control, slope failure can occur. It’s like walking a tight rope. The slope stability calculations are limited by geologic uncertainty, and so, safety factors are required. But how much of a safety factor: 1.5, 2.0, 4.0, or 10? There are analytical methods in rock and soil mechanics to improve the accuracy of your predictions, and the use of risk analysis is standard. Nonetheless, the possibility of a slope failure weighs on the operations and engineering personnel. A clever and necessary approach is to choose a smaller safety factor, but utilize sophisticated slope monitoring instrumentation and techniques to detect the earliest signs of incipient slope failure. Engineering and operational interventions can be initiated immediately to prevent a catastrophic loss.
Optimize cutoff grade and production rate
Mining companies perform market surveys to make an accurate estimation of the amount of product that can be sold every year, and at what price. Remember, the cutoff grade was based on an assumed selling price and an assumed mining cost. As the market changes, the cutoff grade will change, and as production costs change, for better or worse, the cutoff grade will change.
As an example, the annual tonnage that can be sold is suggested by the marketing surveys for a copper mining operation. The annual production rates for the mill and mine are calculated accordingly. Keep in mind that mill production rate only depends on ore, whereas the mine production rate includes both ore and overburden removal. The mining equipment should be selected in such a way that sufficient ore is sent to the mill, and so, there is sufficient capacity to maintain additional faces to satisfy the “sufficient exposure” constraint. There are flexibilities for both ore production and waste mining plans. Moreover, multiple destinations may be considered for the material, including sending material to a waste dump, a low-grade leach dump, a high-grade leach dump, the mill and sometimes an ore stockpile, which is used to feed the mill when mine production is down. Cutoff grades need to be determined for each of these destinations. I imagine that you are beginning to appreciate the need for thorough mine planning to support these decisions — hence, this objective to examine the economic merits of alternative production scenarios, including different ore production rates and cutoff grades, for the purpose of optimizing the cutoff grades and production rates.
Optimize method and equipment selection
Earlier in this module, the importance of selecting the proper size of mining equipment was discussed. We learned that all of the possible options for the fleet should be studied and the best option should be selected. Mining equipment selection is a complex multi-criteria decision-making problem. These parameters include, but are not limited to, the unit cost of the operation, equipment availability, selectivity, operating space, environmental impact, and many other technical and economic parameters. A mine planner should subject the proposed mining strategy, mine development plans, equipment selection, and environmental protection plans to very thorough "what if" contingency planning.
This is also a good time to remind you that mining methods and equipment can evolve and change over the life of a mine. Just because you started out with a specific method and unit operations, does not mean that you have to stick with those for the next 30 years! You may want to change one or both based on new conditions, new technology, and so on. This can only be assessed through ongoing engineering simulations and analyses.
This concludes the summary of mine planning objectives as first outlined by Mathieson. While these eight objectives are timeless in their guidance, i.e., they were true 30 years ago and will be every bit as true 30 years from today, we need to add one additional objective to reflect society’s nascent and evolving value of sustainability.
Develop sustainable mine plans to achieve sustainable mining operations
We talked about sustainability in mining and its importance. If we are to mine in a sustainable manner, then our mine planning must reflect that value. This means taking steps to avoid sterilizing the reserve, maximizing recovery rates, minimizing environmental impact, and ensuring worker safety and health through the design of the mine, the selection of equipment, and the choice of unit and auxiliary operations. Much, but not all of the mining industry has been the vanguard of the triple-bottom line: economic, safe, and environmentally responsible operations. The triple bottom line concept has evolved and changed into the term sustainable operations. It will be your responsibility through mine planning to ensure that the industry continues its journey to sustainable mining in all commodities and in all locations.
Now, armed with an understanding of mine planning, let’s take a look at surface mining methods!