
Lesson 5.4: Drilling
We looked briefly at drills in Lesson 5.1, as part of an overall survey of the unit operations for winning the ore. I showed you some pictures of different types of drills, and we talked about a few drilling applications. Here in this short lesson, I want to approach the topic of drilling more systematically.
Drilling is done for many reasons, and examples include:
- Create a cavity that can be filled with explosives, as part of a blast round.
- Create a hole to install a rock or cable bolt.
- Degas a coal seam, i.e., drain the methane, prior to mining by drilling holes from which the gas can be removed.
- Drill boreholes for solution mining.
- Drill water wells to provide water for the mine, or to monitor groundwater conditions.
- Obtain either cores or cuttings for exploration purposes.
This is a fairly complete list. While the drilling equipment may look differently depending on the application, the principles are similar. Here, we want to focus on the common principles.
Regardless of our reason for drilling, the goal is to penetrate the rock. We are going to focus on mechanical penetration, although there are a tiny number of applications for water jet and thermal penetration. Penetration occurs when we cause a local failure of the rock and remove the failed pieces, known as cuttings, from the hole. Simplistically, the rock fails in compression or tension. Drill bits create one or both of these forces, which causes the rock to fail. Often a given bit design will create predominately one type of force and the other to a lesser extent.
Percussive energy causes failure of the rock in compression. Imagine taking a sharp chisel, placing the edge on a rock, and striking it with a hammer. As you strike the chisel, it is pressed into the rock, and puts the rock underneath the chisel edge in compression. There is some crushing under the chisel edge, but importantly, cracks will propagate outward, and chips of rock will be released. We could strike the chisel with our hammer again, and similar effect will follow, although perhaps not giving us the same degree of fracturing. We could strike a third blow, and while we would see our indentation or groove become slightly deeper, the penetration would be again less. If we want to achieve a better penetration rate, we need to index our chisel bit; i.e., after each strike, we need to rotate the chisel edge by say 15°. This results in dramatically improved penetration. Thus, percussion drills index the bit after each strike. A percussion drill may strike more than once per second, and will index the bit after each strike.
Rotary energy causes failure of rock in tension and shear. Imagine taking our chisel, and while bearing down on the chisel, we also rotate it, dragging the chisel edge across the surface of the rock. In so doing, we will exceed the tensile and shear strength of the rock, and rock fragments will “peel” away. Of course, a mechanical drill will be able to rotate the drag bit much faster than you ever could! Rotation rates may exceed one per second. Intuitively, you probably suspect that rotary methods are only effective with softer materials, and you are correct. Rotary bits with diamond cutters, suitable for use in hard materials, are commercially available, but not normally used in mining applications.
If we wanted to make a broad statement, we could say that the lowest drilling costs are realized by using rotary drag bits in soft materials, rotary-percussion bits in medium hard to hard materials, and percussion bits in very hard materials.
The resistance of the rock to drilling is termed its drilling strength. This is an empirical term used to make comparisons, but it is not quantified in the way we can quantify engineering parameters such as compressive strength or strain, for example. Nonetheless, you will find tables giving the relative drilling strength of different materials, and these tables are informative.
One could spend an entire course on the theory of drilling and rock fragmentation, but for our purposes to utilize drills, there’s not much more that you need to know about the mechanics of rock penetration!
The piece of equipment that we refer to as a “drill” is a system of four components.
- The drill is the power source, which often referred to as the hammer, and the associated frame or carriage, that converts electrical, pneumatic, or hydraulic, internal-combustion energy into percussive and/or rotational energy. Typically, a diesel engine and/or electric motor power either an air compressor or a hydraulic pump, and the high-pressure air or hydraulic fluid directly power a motor to supply energy to the drill bit. In years past, large (huge) air compressor plants were installed on the surface or at main levels underground, and large air distribution networks were installed to provide compressed air to the drills. This would be a rarity today.
- The drill rod, a.k.a. steel, stem, or pipe, transmits the energy from the drill to the drill bit. Remember that this component is not used to transfer power in the case of the down-the-hole drill. This style drill incorporates both the power converter and the bit. Hydraulic fluid or compressed air is provided directly to the down-the-hole drill, which converts the supplied energy to rotary and percussive energy for the drill bit.
- The drill bit is designed to fragment the rock when energy is applied to it.
- Circulation fluid, a.k.a. drilling fluid, flushes the cuttings from the bottom of the hole and cools the bit. If the cuttings are not removed immediately from the hole, they will pack in the bottom and quickly arrest any penetration. Compressed air is often used to remove the cuttings and to provide a modest amount of cooling to the bit. In other cases, water may be used, or occasionally in mining applications, clays and other materials will be mixed with the water to provide improve cooling of the bit and to remove the cuttings from deep holes.
Drill types may be classified by:
- Hammer location
- top hammer
- down-the-hole
- Drilling action
- rotary
- percussion
- rotary-percussion
- Mount or Carriage
- track
- platform
- truck
- Power Source
- diesel engine powering an air compressor, often called “diesel over air”
- electric motor powering a hydraulic pump, often called “electric over hydraulic”
When you are out and about the industry, you will hear people say they have a two-boom jumbo that’s electric over hydraulic, or we’re using an air-track drill in our quarry. These colloquial names are built on this list.
We looked at some pictures of drills in Lesson 5.1. Here I want to show you a few photos of bits.
Here is a cross section of a down-the-hole bit.
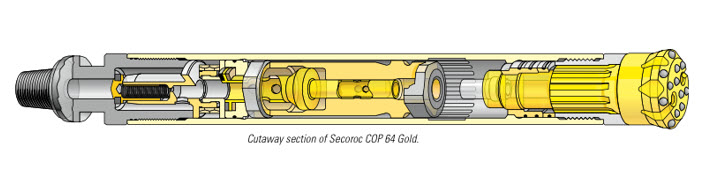
And give it a sense of scale, here is the same bit in the hands of a driller.
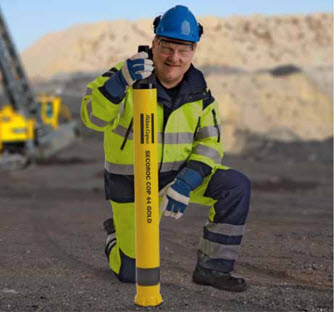
On the left, we have small 2” percussive bit. On the right side, we have a small rotary drag bit.
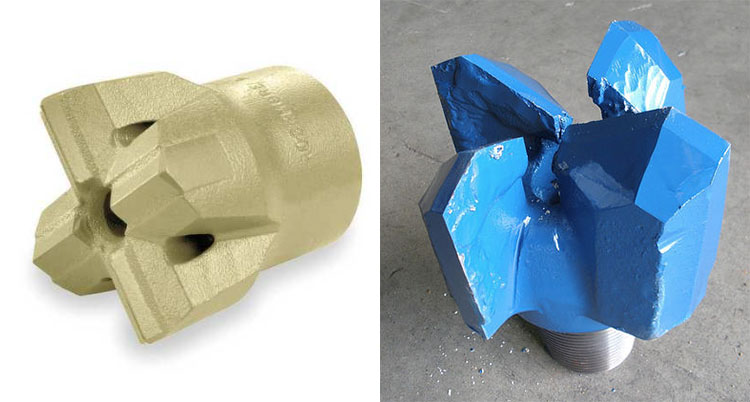
Here is the real workhorse of the drilling industry – the roller tricone bit. Downward force, i.e., thrust, is applied to this bit as well as rotation. As the bit rotates, the individual roller cones are caused to rotate, and then each bit tooth successively impacts the bottom of the hole. These are very effective bits. The size of the teeth on the roller cones will depend on the hardness of the rock. In softer materials, the teeth will be large and wedge shaped. Bits for harder materials will become smaller, and for the hardest materials, the teeth are small buttons or beads. Why do you think the size of the teeth would change?
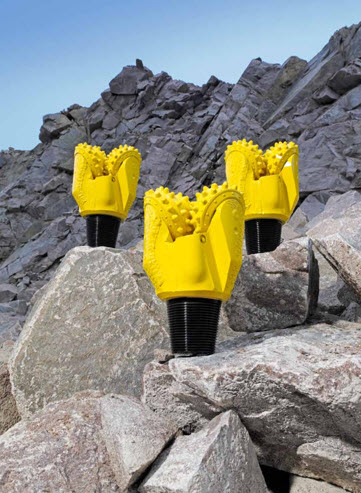
The drilling strength of the rock, i.e., its resistance to penetration, will have a significant effect on the cost of drilling. It is not the only parameter to do so, however. Other factors that will affect drilling performance can be organized into four groups:
Operating Factors
These affect the four components of the drilling system (drill, rod, bit, and fluid).
They are largely controllable and include factors that affect the tools (drill power, blow energy and frequency, rotary speed, thrust, and rod design) and drillhole cleaning (fluid properties and flow rate).
Drillhole Factors
These include hole size, length, and inclination; they are dictated by outside requirements and thus are largely uncontrollable. Hole diameters in surface mining are typically 6 to 18 in. (150 to 450 mm); underground, they typically range from 1.5 to 7 in. (40 to 175 mm).
Rock Factors
These consist of properties of the rock, geological conditions surrounding the rock, and the state of stress acting on the drillhole. Often referred to as drillability factors, they determine the strength of the rock and limit drill performance. Because these factors are a result of the geologic environment, they are largely uncontrollable. Make a note of the importance of the Blast Hole log! We’ll discuss that further when we talking about explosives and blasting.
Service Factors
These variables include labor and supervision, power supply, job site conditions, weather, and so forth. Except for labor and supervision, they are independent factors and cannot often be affected by the drill operator.
The performance metrics for drilling are:
- cost/ft of hole drilled; and
- drilling cost/ ton of material produced
- feet-drilled/ ton of material produced (known as the drillability factor)
You will find all three of these in common use.
Never forget that we strive to optimize the system, not just the subsystems. This it is not just about the drilling cost, but also the associated blasting cost, since we are drilling specifically to conduct blasting. So, a goal is to achieve a low drilling and blasting cost.
I will mention it now for completeness, and we’ll discuss it in the next set of lessons: the typical performance metrics for blasting are:
- cost/ton
- lb-explosive / ton of blasted material or lb-explosive/ ft3 in-place (bank) material blasted (both of these are known as powder factor)
Drillability factor and powder factor are two very important metrics for use to keep track of, in our operations.
Before leaving the performance metrics specifically, and drilling in general, I need to add that it is not just about optimizing drilling and blasting, but what else? Well, loading in particular, and then materials handling, and of course mineral processing. Actions or inactions within any of these can adversely affect the profitability for the mining operation, and our decisions at each step must be informed by a knowledge of the impact of those actions on subsequent operations. This will become clearer as you acquire more and more knowledge throughout this course.