
7.4.1: Dredging or Dredge Mining
A dredge is the principal piece of equipment used in the dredging method and, essentially, a dredge is a boat containing specialized mining and materials handling components. Accordingly, a dredge requires a body of water in which to operate. In many cases, this is a natural body of water such as a river or a lake, but in others, it is a manmade pond or small lake. Of course, the only reason for floating a dredge is to recover something of value at the bottom of this body of water. We need to add one more condition, and that is: the material of value on the bottom must be unconsolidated, such as sand and gravel, or it must be very soft. Simplistically, the dredge is designed to lift these materials of interest from the bottom up into the dredge. Shortly, we will look at how the payload is moved in a little more detail, but for now, let’s talk for a moment about the kinds of materials that are typically recovered with this method, dredging or dredge mining.
The bottom of rivers, lakes, and harbors is often a good source of gravel. Gravel can be used sometimes in concrete as well as for a variety of other purposes such as architectural and landscaping purposes. Dredging to remove this material has the additional benefit of deepening the channel or harbor, and sometimes that is the primary purpose of dredging, and the recovery of minerals is a secondary benefit… the “icing on the cake,” so to speak!
Glaciers once covered a significant portion of the Earth’s surface, and the movement of these glaciers created extensive unconsolidated deposits of materials containing not only sand and gravel, but gold, tin, diamonds, and other heavy minerals. These alluvial deposits created by glaciation, are also known as placers. I mention this here because you will sometimes hear or read about placer mining or alluvial mining. Although these terms may be used interchangeably with dredging or dredge mining, you can’t assume that to be true in all cases. As we will see, hydraulic mining may be used in these deposits as well. Regardless, if we have a body of water covering a placer deposit, we will consider strongly using dredge to recover the minerals of interest.
Moreover, if we have such a deposit that is not underwater, but is in an area that could be easily flooded, we will consider making our own lake and then using a dredge to recover the bottom materials. If the deposit is in an area with a very shallow water table, we may simply have to remove several feet of overburden, e.g., vegetation and soil, and the excavated area will fill with water on its own. Then, we can float the dredge and mine the deposit. There are other circumstances where we could create a manmade lake to mine the deposit, but it a complicated process, because we cannot take any action that could have an adverse environmental impact.
Let’s talk a bit more about the dredge itself. A dredge is defined by the way in which it recovers the ore from the bottom. The four types are bucket-wheel, ladder, clamshell, and suction. The choice will depend on the depth of the deposit below the surface of the water and the degree of consolidation of the deposit. The size of the dredge will depend on the desired production rate and the characteristics of the body of water, e.g., depth and extent. Let’s start by looking at a picture of a dredge.
This is a large dredge, and specifically, it is a bucket-wheel dredge. You can see the bucket wheel on the left side of the picture. The bucket wheel rotates, digging into the soft material at the bottom. The dug or “mined’ material is then transfer onto the dredge. Typically, some sort of a gravity separation is employed to segregate the material of interest from the silt, mud, and other detritus of no interest. The latter is then immediately returned to the water.
The bucket-ladder dredge is probably the most common type of dredge, as it is the most flexible method for dredging under varying conditions. The excavation equipment consists of an endless chain of open buckets that travel around a truss or “ladder.” The lower end of the ladder rests on the mine face—that is, the bottom of the water where excavation takes place—and the top end is located near the center of the dredge. The chain of buckets passes around the upper end of the ladder at a drive sprocket and loops downward to an idler sprocket at the bottom. The filled buckets, supported by rollers, are pulled up the ladder and dump their load into a hopper that feeds the separation plant on the dredge. After the valuable material has been removed, the waste is dumped off the back end of the dredge. Here is a picture of a bucket-ladder dredge, which gives a clear front view of the bucket ladder.
Here is a view of a bucket-ladder dredge used to mine phosphate.
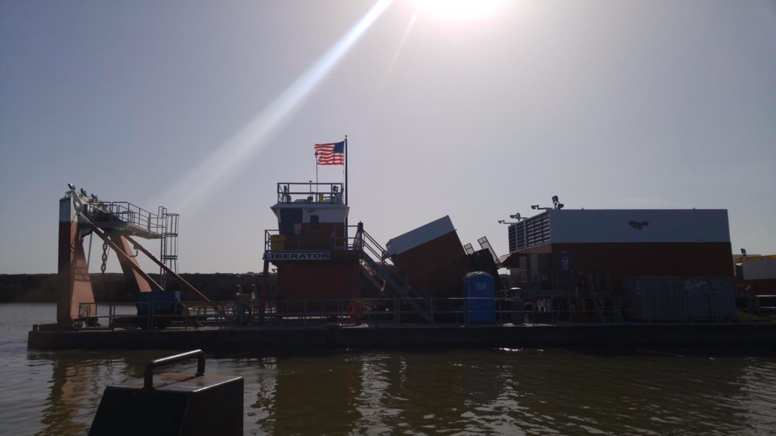
And here is that same dredge in a photo taken from a distance.
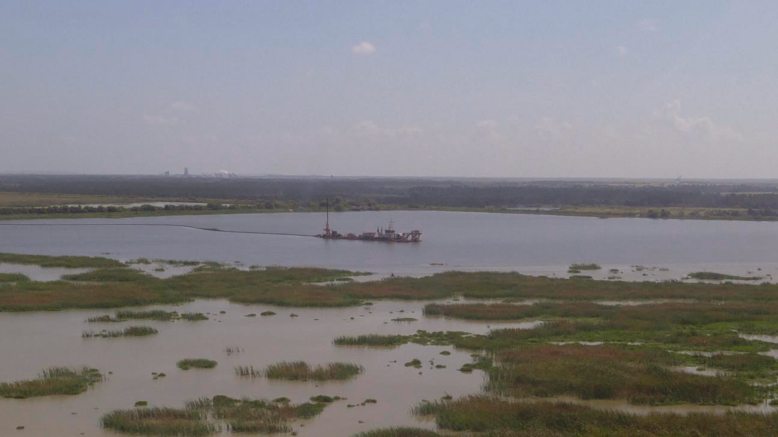
Finally, here a view from the operator's cab of that dredge. Notice the computer displays providing not only video images of different parts of the dredge but also sensor data that the operator can use to better control the operation of the dredge.
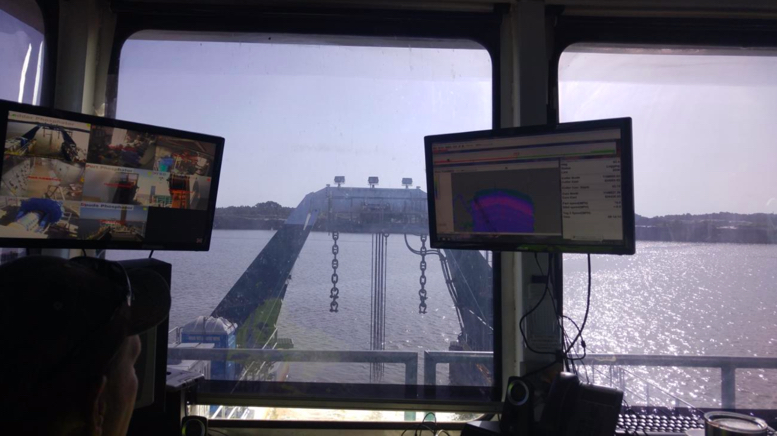
The clamshell dredge, unlike the previous two, employs a batch rather than continuous process. This type of dredge utilizes a clamshell bucket that is dropped to the bottom, scoops a bucket of material, and is hoisted back to the dredge where the bucket is dumped. This dredge can operate in deeper water than other systems and handles large material, e.g., larger rocks, well. A typical cycle time would be on the order of one minute, depending on the depth of the water. You understand the drawback of batch or discontinuous systems, and consequently, this style of dredge would only be used when its unique strengths are necessary. A typical clamshell dredge is shown here. Note the ability of this style dredge to place its payload on the dredge or on a nearby barge or structure.
The fourth type of dredge is a hydraulic dredge. Imagine a big vacuum cleaner with a long hose – the hose is dropped to the bottom, the “vacuum” is turned on, and the material is literally sucked up the hose and captured on the dredge. Basic physics limits the amount of “lift” that can be achieved. However, the amount of lift can be supplemented with a high-pressure spray around the suction nozzle – essentially a push-pull system. This is known as hydrojet assistance. This style of dredge is suited to digging relatively small-sized and loose material such as sand and gravel, marine shell deposits, mill tailings, and unconsolidated overburden. Hydraulic dredging has also been applied to the mining of deposits containing diamonds, tin, tungsten, niobium-tantalum, titanium, and monazite. This figure diagrammatically illustrates the use of a suction dredge. Note that the use of a hydraulic pipeline to move material off the dredge is often associated with the use of this type of dredge.
This picture shows a very small suction dredge, which might be used to clear a tailings pond, for example.