
Catalytic Reforming
Catalytic reforming converts low-octane, straight-run naphtha fractions, particularly heavy naphtha that is rich in naphthenes, into a high-octane, low-sulfur reformate, which is a major blending product for gasoline. The most valuable byproduct from catalytic reforming is hydrogen to satisfy the increasing demand for hydrogen in hydrotreating and hydrocracking processes. Most reforming catalysts contain platinum as the active metal supported on alumina, and some may contain additional metals such as rhenium and tin in bi- or tri-metallic catalyst formulations. In most cases, the naphtha feedstock needs to be hydrotreated before reforming to protect the platinum catalyst from poisoning by sulfur or nitrogen species. With the more stringent requirements on benzene and the total aromatics limit for gasoline in the United States and Europe, the amount of reformate that can be used in gasoline blending has been limited, but the function of catalytic reforming as the only internal source of hydrogen continues to be important for refineries.
Figure 8.1 locates the catalytic reforming process in a refinery. The feedstock for catalytic reforming is straight-run (directly from the crude oil) heavy naphtha that is separated in the naphtha fractionator of the Light Ends Unit, as discussed in Lesson 4. Light naphtha from the naphtha fractionator, inherently a low-octane-number fraction, can be sent directly to blending in gasoline pool after hydrotreating, if necessary, or sent to an isomerization process to increase its octane number. As discussed in Lesson 3, hydrotreating heavy naphtha is often necessary before catalytic reforming to protect the noble metal catalyst (e.g., Pt) used in the reforming process. The intended product from catalytic reforming is the high-octane-number reformate and the most significant by-product is hydrogen gas.
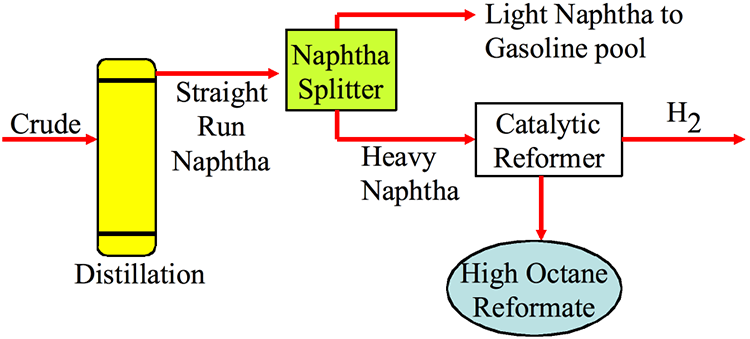