
Alkylation
The alkylation process combines light iso-paraffins, most commonly isobutane, with C3–C4 olefins, to produce a mixture of higher molecular weight iso-paraffins (i.e., alkylate) as a high-octane number blending component for the gasoline pool. Iso-butane and C3–C4 olefins are produced as by-products from FCC and other catalytic and thermal conversion processes in a refinery. The alkylation process was developed in the 1930s and 1940s to initially produce high-octane aviation gasoline, but later it became important for producing motor gasoline because the spark ignition engines have become more powerful with higher compression ratios that require fuel with higher octane numbers. With the recent restrictions on benzene and the total aromatic hydrocarbon contents of gasoline by environmental regulations, alkylation has gained favor as an octane number booster over catalytic reforming. Alkylate does not contain any olefinic or aromatic hydrocarbons.
Alkylation reactions are catalyzed by strong acids (i.e., sulfuric acid [H2SO4] and hydrofluoric acid [HF]) to take place more selectively at low temperatures of 70°F for H2SO4 and 100°F for HF. By careful selection of the operating conditions, a high proportion of products can fall in the gasoline boiling range with motor octane numbers (MONs) of 88–94 and RONs of 94–99 [15]. Early commercial units used H2SO4, but more recently, HF alkylation has been used more commonly in petroleum refineries. HF can be more easily regenerated than H2SO4 in the alkylation process, and HF alkylation is less sensitive to temperature fluctuations than H2SO4 alkylation [3]. In both processes, the volume of acid used is approximately equal to the volume of liquid hydrocarbon feed. Important operating variables include acid strength, reaction temperature, iso-butane/olefin ratio, and olefin space velocity. The reactions are run at sufficiently high pressures to keep the hydrocarbons and the acid in the liquid phase. Good mixing of acid with hydrocarbons is essential for high conversions.
Some examples of desired alkylation reactions (combination of iso-paraffins with olefins) are given in Figure 8.6. These occur through ionic chain reactions (Figure 8.7) initiated by donation of a proton from the acid catalyst to an olefin to produce a carbocation that reacts with iso-butane to form a tert-butyl cation. Subsequent propagation reactions involve the reactions of a tert-butyl cation with olefins to form larger iso-paraffin cations that lead to final products through reactions with iso-butane to form a new tert-butyl cation to sustain the chain reaction [3]. The alkylation reaction is highly exothermic; therefore, cooling the reactor contents during alkylation is important.
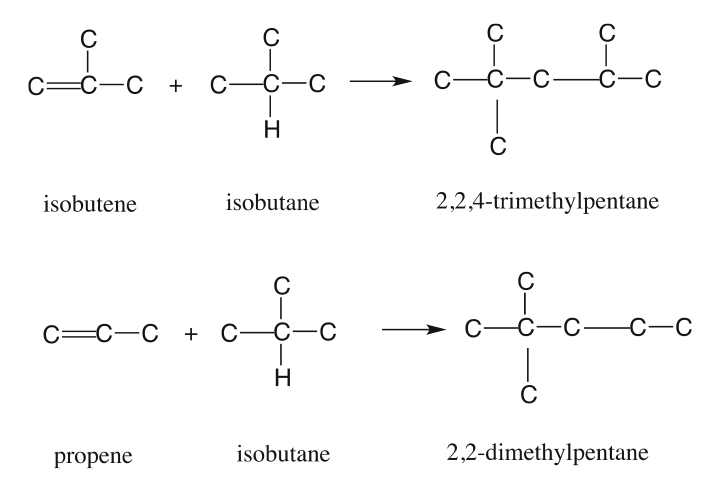
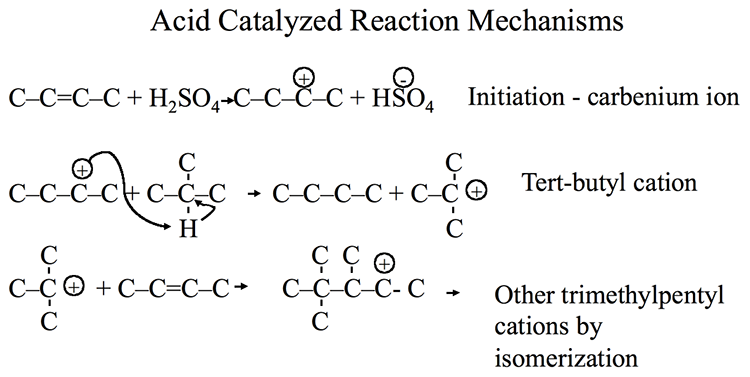