
5.3.2: Continuous Miners for Noncoal Applications
The impetus for developing the continuous miner came from the coal mines, but their application has grown beyond coal. The motivation for using them in noncoal mines is the same: eliminate delays wherever possible. In the case of the metal/nonmetal mines, the desire is to eliminate the discrete unit operations of drilling, blasting, and loading, along with the attendant delays. Unfortunately, there is a practical limitation that cannot be overcome in many cases. It is the hardness of the ore. The carbide cutting bits must be able to penetrate and fracture the ore, and do so with some speed and without destroying the bits in a short period of time. The limit is currently a compressive strength of around 80 MPa. This means, for example, that coal, salt, trona, potash, and some copper deposits are suitable, whereas most limestone and lead/zinc deposits are not. Pushing that limit ever higher is the goal of researchers, manufacturers, and the mining companies.
The structure and appearance of the continuous miner will change somewhat for those machines designed for use in harder rock deposits. The miner shown in the picture below looks similar to the one designed for operation in a coal mine, but there are a few subtle and important differences. The size of the machine reflects the thicker deposit in which this machine will be used, the structure is reinforced, and the lacing pattern of the bits is different – larger but fewer bits to concentrate the available energy to achieve fragmentation of the harder rock.
As the hardness of the rock increases, the cutting head will become much smaller, but for the same reason – concentrate more energy into a small area of the rock. Look at what’s happened to the size of the cutting head on this machine. The arm, on which the cutting head is mounted, has the ability to swing and extend. Note the bit marks in the top of the deposit. This configuration of continuous miner is often known as a roadheader, which is based on its European heritage and its use in driving gateroads. Also, take note of the size of the gathering pan and the two gathering arms.
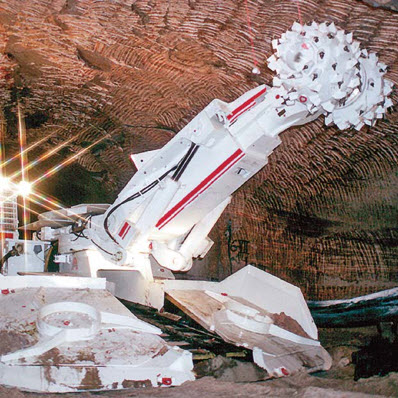
With this overview of continuous miners behind us, we can now return to this question of the shuttle car, and what to do about the inherent delay. Well, it turns out that this is really part of a larger and age-old problem: batch versus continuous haulage.