
8.4.2c Longwall Mining
Longwall mining applies to thin, bedded deposits, with uniform thickness and large horizontal extension. Typical deposits are coal seams, potash layers or conglomerates, trona, and gold reefs. Longwalls are found in nearly horizontal deposits of coal and trona, whereas in metal/nonmetal deposits, a steeper dip is tolerated. The difference is in the equipment that is used. Coal and trona are using massive suites of mechanized and semi-automated equipment that is unsuitable for use in greater than 5-10% grades. There are exceptions, but we’re not going to complicate this discussion with those.
Longwall mining takes its name from the characteristic long face or wall, which may be several hundred feet or more in length. The figure below illustrates this nicely. The ore is extracted in a slice along this long wall. The region adjacent to the face is kept open, i.e., free of obstructions, to allow space for miners and equipment. This region might extend 10’-20’ out from the wall. If we are looking at mining a gold reef, for example, a line of posts will be installed to support the roof or back and protect the active mining activity. At some distance back from the face, caving will be allowed to occur, and in most instances, this is necessary to relieve superimposed loads on the working face. If we are looking at a coal application, the process will be somewhat different. A significant percentage of the coal that is mined underground comes from longwall mines; and not just in the U.S. but around the world. As such, we’ll look more closely at longwall mining in coal.

Longwall Mining of Coal
Longwall mining of coal is a high production and high productivity method, employing sophisticated electrical, mechanical, and hydraulic systems, as well as computer-based monitoring and control systems. Most modern (coal) longwall faces are semi-automated. It is noteworthy that longwall operations in trona mines utilize essentially the same equipment and processes that are used in coal mine longwalls. As the long wall or face is mined and the roof supports advance forward with mining, the roof in the mined-out area will cave.
When the panel is initially mined, caving will be delayed. This is a worrisome period because all of the weight of the unsupported roof is transferred to the face and also the gateroad pillars. Sometimes caving may not start for 10 - 20 or more passes of the shearer. If the superimposed load becomes too great, the face and pillars can begin to crush. Thus, for longwall to work safely and productively, the cave must occur in a timely fashion. Once it has started to cave, it will generally continue with each pass of the shearer. Ground control experts will conduct a cavability analysis of the overburden before a decision is made to employ this mining method. This requirement for caving is the reason this method is classified in the caving class of methods.
Please be aware that the longwall panels within the coal deposit are created by room and pillar mining. Thus, many room and pillar (coal and trona) mines are also longwall mines, and in most of them, the room and pillar work is simply to develop the panels and the infrastructure to facilitate operation of the longwall. By that, I mean you need to have a well-developed ventilation, materials handling, and power systems to support a high production longwall. The room and pillar mining creates the mains, submains, and panel entries for these systems. Let’s look at a few figures. These won’t answer all of your questions right now, but these in combination with some videos that will come afterwards, should give you a good understanding of the method.
Let’s start with a plan view of a mine. This figure, below, shows a portion of the mains or submains and the longwall panels. Notice the three-entry gateroads that define the panels. One set of these will be known as the headgate entries and the other as the tailgate entries. The one of the longwall face will be known as the headgate and the other end of the face will be known as the tailgate. The entries adjacent to the mined out panel are the tailgate entries, and that defines the tailgate side of the panel. The longwall face is mined on retreat. That is to say, the gateroads are mined on advance, and then the longwall face retreats back to the submains or mains.

The equipment required for a longwall face is unique to this mining method. Let’s look at it in this figure below, and then when you see it in the videos, it will make more sense.

The armored face conveyor is a massive steel structure containing a chain conveyor. The shearer (or plow) rides on the AFC and cuts the coal. The cut coal falls into the AFC, and is transported to the headgate. At the headgate, the coal is crushed to a size suitable for transport on a conveyor belt and then fed at a controlled rate onto the belt. This panel belt feeds the outby belt system. It takes an enormous amount of power (1000s of hp) to operate the AFC, and there are drives at both the tail and headgates to power the chain conveyor. All of this equipment and the miners working at the face are protected by what has been called an umbrella of safety, i.e., the series of shields. As the coal is cut, the AFC snakes into place immediately adjacent to the face. On the right side of this figure, they are depicting this advance of the face, and you can see the shields that have moved into place.
This next figure illustrates more completely the relationship of the longwall panel to the overburden, the gateroads, and the longwall face itself.
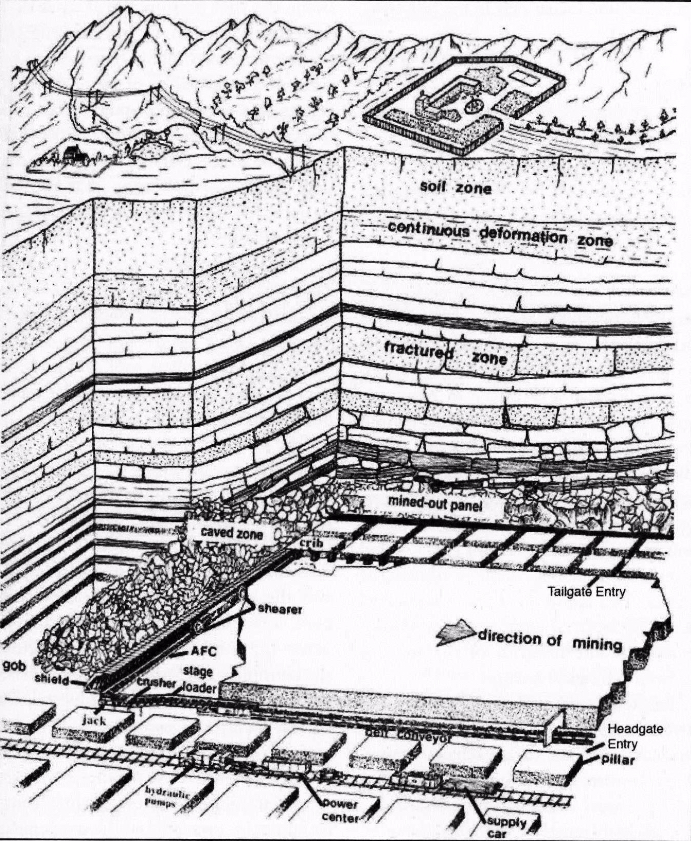
Next, let’s take a look at some videos, each of which is less than five minutes in length. I think these videos are helpful for the details that they show. There are four of them, and they are addressing the same basic topic. However, in each one you can see certain important details more clearly than in the other videos. I suggest that you watch all of them twice, and don’t hesitate to pause them and look more closely at the image. In so doing, you’ll develop a more complete understanding of the equipment and the process.
I want to make one correction to the videos. Caterpillar or CAT as it is known, is a global manufacturer of excellent mining equipment. One important detail of their second video is not quite correct, however. All longwalls in the U.S. use shearers, not plows, including the longwalls operating in thin seams. The reasons for this are not important here, but please remember that shearers, not plows are applied through the U.S coal fields. In MNG 410, we take a more detailed look at longwall mines, including the conditions that favor the use of the plow.
I imagine that you have a reasonable understanding of modern longwall mining after studying the figures and the videos. Allow me to summarize the process and add a few additional details of interest.
Development of the panels is done with the room and pillar method. It generally will take at least two continuous mining sections to develop the longwall panels. From a mine planning perspective, the goal is to ensure that you have panels developed and ready to go. Often, the mine will have spare longwall equipment, and they will partially set up a longwall face on the next panel, so that minimal time will be lost in moving to the next panel and commencing with longwall production. This requires that panel development activities stay far enough ahead of the longwalls to ensure that the next panel can be set up before mining of the previous panel is completed. However, it is important that panel development does not get too far ahead, which would result in developed panels sitting idle for several months. This would represent a poor use of resources, but more importantly, the roof rock often begins to deteriorate when exposed to the moist mine atmosphere. This could result in roof problems before you have begun to mine in those panels.
Services to the longwall face will be placed in the headgate entries. This includes the panel belt, the staged loader and crusher, the hydraulic pumps for the shields, the electrical power centers, the computer control boxes, and the refuge chamber.
The tailgate is under additional roof stresses, and requires additional roof support, such as concrete pillars, timbered crib structures, and so on.
The number of gate roads is typically three, which is a legal requirement in the U.S. Under severe ground pressures, fewer gate entries are advantageous. In the western U.S., a few mines have received special permission to have only two gate roads. Outside of the U.S., you will find single entry gate roads. A reduction in the number of gateroads does create safety hazards that must be managed.
Panel Development
- Develop the gate roads (headgate and tailgate).
- Connect the headgate and tailgate.
- Develop (mine) the setup rooms – the entries connecting the head and tail gate, are mined to specific dimensions and in a pattern to facilitate setting up the long face of equipment.
- Develop (mine) the recovery rooms – once the longwall has been mined, the longwall face of equipment must be moved to the next panel. Given the size of the equipment, additional openings are mined to facilitate the removal of the face equipment. Finish the setup of the equipment on the new panel.
Production Cycle
The basic production cycle is straightforward, as you no doubt saw in the videos. The cutter, whether a plow or shearer, mines along the width of the face. As the cutter moves, the shields advance forward. As they advance forward, the AFC is pushed to the face; and as such, it is ready for the next cut. A few details that are not apparent would include:
- Mining along the face can always be done in the same direction, e.g., headgate to tailgate, which is known as unidirectional cutting, or it can be done in both directions, known as bidirectional cutting.
- Beginning the cutting cycle at either gate is a multi-step process, requiring that the shearer cut into the gateroad, and then gradually cut into the face over a few hundred feet to reach its full cutting depth, returning back to the gate, and then commencing with a full web cut along the full face.
- The shields are lowered to move forward, and when in the new position, the canopy is extended. Usually, the shields will push into the roof momentarily to aid in the formation of a crack in the roof, which facilitates the caving action. The roof typically does not cave immediately after the shield advance, but once caving has begun, the roof will cave reasonably close behind the shields.
Closing Comments
Modern longwall mining systems represent the highest level of technology and engineering achievement in mining method design. The design of the individual components has pushed the envelope on electrical, mechanical, and hydraulic component design. The productivity of these systems is unrivaled, and the raw tonnages achievable per shift are staggering compared to what was state-of-the-art 20 years ago. As cutting technology advances to allow continuous cutting of harder materials, you will see these systems applied in other commodities… but only if what is true?
This brings us to the end of our discussion of the supported and caving classes of underground mining methods.