
Transportation Process and Flow
Like all energy sources, natural gas has to be available at the point of use. As a gas, the low density of natural gas presents special challenges for transportation. Because of its volume, it is not easily stored or moved by vehicle. For transportation across land, natural gas is usually moved through a network of pipelines. For transport across bodies of water, it is liquefied and carried by ship. The map below from the EIA shows the pipeline network in the U.S.
One if by Land
The section below describes the major components of the natural gas pipeline system in the United States. Most of the content has been excerpted from About U.S. Natural Gas Pipelines - Transportation Process and Flow. (If you would like more information and far more detail, you are encouraged to consult this source.)
The Natural Gas Gathering System
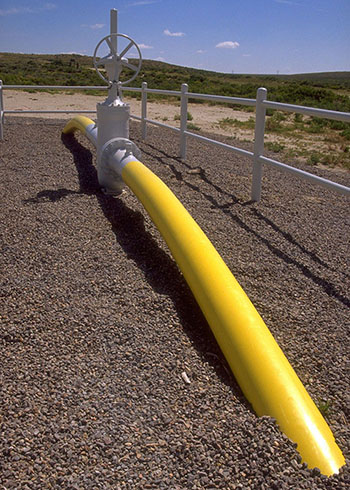
A natural gas pipeline system begins at a natural gas producing well or field. In the producing area many of the pipeline systems are primarily involved in "gathering" operations. That is, a pipeline is connected to a producing well, converging with pipes from other wells where the natural gas stream may be subjected to an extraction process to remove water and other impurities if needed. Natural gas exiting the production field is usually referred to as "wet" natural gas if it still contains significant amounts of hydrocarbon liquids and contaminants. . . .
Once it leaves the producing area, a pipeline system directs flow either to a natural gas processing plant or directly to the mainline transmission grid. Non-associated natural gas, that is, natural gas that is not in contact with significant quantities of crude oil in the reservoir, is sometimes of pipeline-quality after undergoing a decontamination process in the production area, and does not need to flow through a processing plant prior to entering the mainline transmission system.
The Natural Gas Processing Plant
At the wellhead, natural gas is usually a mix of mostly methane along with other hydrocarbons including ethane, propane, butane, and pentanes. Raw natural gas also contains water vapor, hydrogen sulfide (H2S), carbon dioxide, helium, nitrogen, and other compounds. This is why natural gas is sent to a processing plant after being extracted.
The principal service provided by a natural gas processing plant to the natural gas mainline transmission network is that it produces pipeline-quality natural gas. Natural gas mainline transmission systems are designed to operate within certain tolerances. Natural gas entering the system that is not within certain specific gravities, pressures, Btu content range, or water content level will cause operational problems, pipeline deterioration, or even cause pipeline rupture.
In processing, associated hydrocarbons (e.g., ethane, propane, butane, and pentanes) are removed and captured from natural gas and are known as "natural gas liquids " (NGLs), valuable by-products of natural gas processing. Natural gas processing plants also extract contaminants from the natural gas stream to produce pipeline quality "dry" gas, which is transported to end-users. "Dry" or "consumer grade" gas is almost pure methane and is what is used by consumers.
The Transmission Grid and Compressor Stations
The natural gas mainline (transmission line) is a wide-diameter, often-times long-distance, portion of a natural gas pipeline system, excluding laterals, located between the gathering system (production area), natural gas processing plant, other receipt points, and the principal customer service area(s). The lateral, usually of smaller diameter, branches off the mainline natural gas pipeline to connect with or serve a specific customer or group of customers. . . .
Between the producing area, or supply source, and the market area, a number of compressor stations are located along the transmission system. These stations contain one or more compressor units whose purpose is to receive the transmission flow (which has decreased in pressure since the previous compressor station) at an intake point, increase the pressure and rate of flow, and thus, maintain the movement of natural gas along the pipeline. . . .
To address the potential for pipeline rupture, safety cutoff meters are installed along a mainline transmission system route. Devices located at strategic points are designed to detect a drop in pressure that would result from a downstream or upstream pipeline rupture and automatically stop the flow of natural gas beyond its location.
Natural Gas Market Centers/Hubs
Natural gas market centers and hubs evolved, beginning in the late 1980s, as an outgrowth of natural gas market restructuring and the execution of a number of Federal Energy Regulatory Commission’s (FERC) Orders culminating in Order 636 issued in 1992. Order 636 mandated that interstate natural gas pipeline companies transform themselves from buyers and sellers of natural gas to strictly natural gas transporters. Market centers and hubs were developed to provide new natural gas shippers with many of the physical capabilities and administrative support services formally handled by the interstate pipeline company as “bundled” sales services.
Two key services offered by market centers/hubs are transportation between and interconnections with other pipelines and the physical coverage of short-term receipt/delivery balancing needs. . . .
Underground Storage Facilities
At the end of the mainline transmission system, and sometimes at its beginning and in between, underground natural gas storage and LNG (liquefied natural gas) facilities provide for inventory management, supply backup, and the access to natural gas to maintain the balance of the system. There are three principal types of underground storage sites used in the United States today: depleted reservoirs in oil and/or gas fields, aquifers, and salt cavern formations. In one or two cases mine caverns have been used. Two of the most important characteristics of an underground storage reservoir are the capability to hold natural gas for future use, and the rate at which natural gas inventory can be injected and withdrawn (its deliverability rate). . . .
Peak Shaving
Underground natural gas storage inventories provide suppliers with the means to meet peak customer requirements up to a point. Beyond that point the distribution system still must be capable of meeting customer short-term peaking and volatile swing demands that occur on a daily and even hourly basis. During periods of extreme usage, peaking facilities, as well as other sources of temporary storage, are relied upon to supplement system and underground storage supplies.
Peaking needs are met in several ways. Some underground storage sites are designed to provide peaking service, but most often LNG (liquefied natural gas) in storage and liquefied petroleum gas such as propane are vaporized and injected into the natural gas distribution system supply to meet instant requirements. Short-term linepacking is also used to meet anticipated surge requirements.
The use of peaking facilities, as well as underground storage, is essentially a risk-management calculation, known as peak-shaving. The cost of installing these facilities is such that the incremental cost per unit is expensive. However, the cost of a service interruption, as well as the cost to an industrial customer in lost production, may be much higher. In the case of underground storage, a suitable site may not be locally available. The only other alternative might be to build or reserve the needed additional capacity on the pipeline network. Each alternative entails a cost.
A local natural gas distribution company (LDC) relies on supplemental supply sources (underground storage, LNG, and propane) and uses linepacking to "shave" as much of the difference between the total maximum user requirements (on a peak day or shorter period) and the baseload customer requirements (the normal or average) daily usage. Each unit "shaved" represents less demand charges (for reserving pipeline capacity on the trucklines between supply and market areas) that the LDC must pay. The objective is to maintain sufficient local underground natural gas storage capacity and have in place additional supply sources such as LNG and propane air to meet large shifts in daily demand, thereby minimizing capacity reservation costs on the supplying pipeline (About U.S. Natural Gas Pipelines - Transportation Process and Flow).
Two if By Sea
When natural gas is cooled to about -260°F, it becomes a liquid and, cleverly, is called Liquefied Natural Gas or LNG. In this form, it takes up about one six hundredth the volume of gaseous natural gas.
This has clear advantages for transportation and storage. Because it is easier to move, LNG can give "economically stranded" natural gas deposits access to markets.
LNG is shipped in specialized tankers with insulated walls. This makes it possible for countries that are separated by large bodies of water to import and export gas to one another.
LNG also makes it possible to store quantities of natural gas economically at sites where geologic conditions are not suitable for underground gas storage. This is especially important when LNG is stored at peak-shaving facilities, where it can be gasified and added to pipelines to meet consumer needs at times of peak demand. The videos below provide a good overview of the LNG production chain, including the liquefaction process. (Note that both videos have a closed-captioning option, and a link to the transcripts is available as well.) Please watch the following (3:44) and (2:23) videos:
PRESENTER: LNG, Liquefied Natural Gas. LNG is natural gas that has been cooled to at least minus 162 degrees Celsius to transform the gas into a liquid for transportation purposes.
To understand why liquefying natural gas is important, we first need to understand natural gas's physical properties. Methane has a very low density and is therefore costly to transport and store. When natural gas is liquefied, it occupies 600 times less space than as a gas.
Normal gas pipelines can be used to transport gas on land or for short ocean crossings. However, long distances and overseas transport of natural gas via pipeline is not economically feasible. Liquefying natural gas makes it possible to transport gas where pipelines cannot be built, for example, across the ocean.
The four main elements of the LNG value chain are, one, exploration and production, two, liquefaction, three, shipping, four, storage and regasification. At the receiving terminal, LNG is unloaded and stored before being regasified and transported by pipe to the end users.
The demand for LNG is rising in markets with limited domestic gas production or pipeline imports. This increase is primarily from growing Asian economies, particularly driven by their desire for cleaner fuels and by the shutdown of nuclear power plants.
The largest producer of LNG in the world is Qatar with a liquefaction capacity in 2013 of roughly one-quarter of the global LNG production. Japan has always been the largest importer of LNG and in 2013 consumed over 37% of global LNG trade.
The extraction process also has environmental and social issues to consider. LNG projects require large energy imports for liquefaction and regasification and therefore have associated greenhouse gas emissions.
Spills pose concerns to local communities. There have been two accidents connected to LNG. But in general, liquefaction, LNG shipping, storage, and regasification have proven to be safe. LNG projects require large upfront capital investments, which can be a challenge in moving projects ahead.
That's LNG.
PRESENTER: Heat and cold, Shakespeare told us to fear no more the heat of the sun nor the furious winter's rages, and natural gas now rises above other fuels to beat those forces back.
Natural gas is abundant, at least in some parts of the world, but how do we get it from regions that have it to regions that don't.? So we cool natural gas until it condenses into a compact liquid. Now we can ship it on special tankers.
Natural gas is mostly methane, with varying amounts of other hydrocarbons and impurities that can freeze and foul equipment. We remove the impurities in the pretreatment area of the LNG plant. Here we also remove heavy hydrocarbons, inert gases, and other gases that accompany the methane that is natural gas.
Now we can begin to liquefy this clean gas. Many technologies can do that, but also based on the same cyclic process that serves our kitchen refrigerators. That means we need some kind of refrigerant to remove heat from the gas, so it'll condense into liquid. Here's how it works.
First, the liquid refrigerant expands from a high pressure to a low pressure, turning it into a cold mixture of liquid and some vapor. Next, it passes through a heat exchanger that uses heat from the natural gas to turn the refrigerant into pure vapor. The natural gas is now a lot colder, and we can compress the refrigerant back to its high pressure. We cool the hot refrigerant in another heat exchanger until it condenses back into liquid, then we expand the refrigerant again to repeat the cycle.
The key to cooling condensing natural gas into LNG is flashing the liquid refrigerant. And once the gas is LNG, we store it in tanks at very nearly atmospheric pressure. Liquid natural gas looks like water, except that it boils off at room temperature. It's odorless, colorless, non-toxic, and virtually non-flammable.
The cryogenic LNG stays in these storage tanks at a constant temperature between minus 159 and 162 Celsius. Evaporation helps keep it cool and liquid while it's stored on land or in the ship. We capture the vapors and either burn them for fuel or we re-condense them and send them back to storage. Who then uses the LNG? Typically, a power plant or industrial user, they convert the liquid back to a gas, so it can be burned as a fuel or used as a feedstock.
More than half of today's LNG comes from just four countries-- Qatar, Indonesia, Australia, and Malaysia, but that's soon likely to shift. New natural gas discoveries promised to send Australia, the US, and Africa to the forefront.
The companies that build these plants have much to think about. Who will buy their gas? How best to meet buyer specifications. How much LNG will buyers want? Another thing, buyers have to make long-term commitments before suppliers can invest in new units.
If this is a golden age for natural gas, it rests upon vast ingenuity and daring. What gulfs of heat and cold we must cross to provide that Elixir of warmth anywhere in the world.
To Read Now
- Read "Liquefied Natural Gas (LNG)" from the U.S. Department of Energy's Office of Fossil Energy.
- For some insight into the recent and projected global LNG market, read the 2023 Shell LNG Outlook. Note in particular how the Russia-Ukraine conflict has affected the global LNG market.
- LNG is not embraced by everyone. Read "Canada’s LNG dreams fade as blockades add new costs to industry" by Kevin Orland for some insight into some recent nonmarket action in Canada.
Optional Reading
- Browse through "LNG Monthly" and "Summary of LNG Export Applications" from the Office of Fossil Energy. (These are both linked to in the article above.)
- See "U.S. Liquefied Natural Gas Exports, A Primer on the Process and the Debate" (Center for American Progress). This is an older reading, so the statistics are a little outdated, but the description of the process and other considerations are accurate.
The map below, Major Trade Movements 2021, is from BP Statistical Review of World Energy 2022 (page 36). For a larger version of the map and more information (you may need to do this for this week's questions), please see the original source.
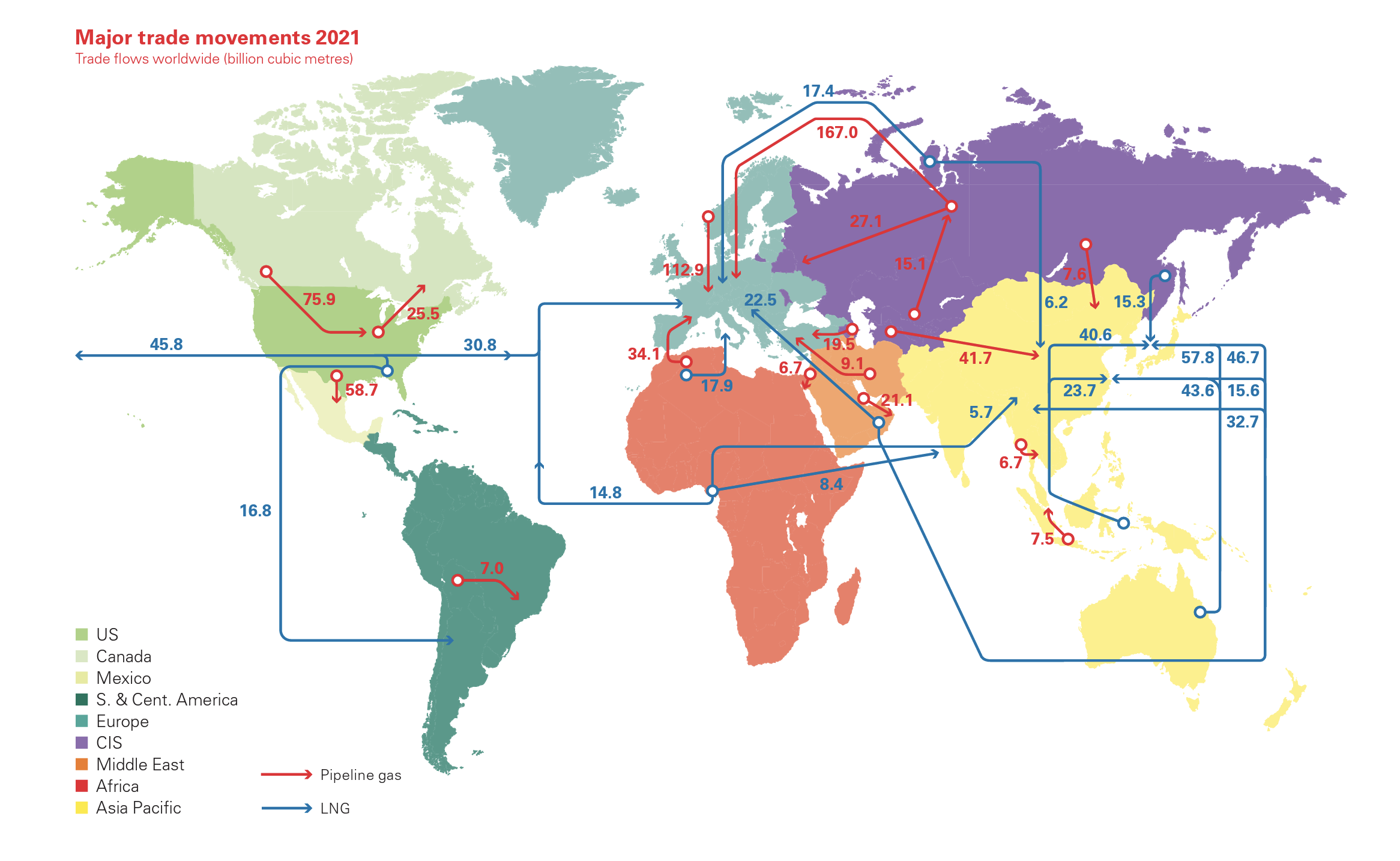