
Houdry Catalytic Cracking
The first catalytic cracking process was developed as a batch process (McAfee, 1915) shortly after the development of a thermal cracking process. The process used Lewis acid catalysts (e.g., AlCl3) for cracking. These catalysts were expensive and corrosive. In addition to these impediments, use of a batch reactor in the McAfee process did not allow large-scale commercialization of this process. The first full-scale commercial process, the Houdry Catalytic Cracking, used much less expensive catalysts, such as clays, and natural alumina and silica particles. Figure 7.5 shows the configuration of the Houdry Catalytic Cracking process. For cracking, gas oil feed was heated to 800°F and fed to a fixed-bed reactor packed with the catalyst particles. Cracking products are sent to a fractionator to be separated into gas, gasoline, light cycle oil (LCO) and heavy cycle oil (HCO) products.
Video: Houdry Catalytic Cracking (5:03)
INSTRUCTOR: As I mentioned before, the evolution of catalytic cracking processes is really a good example of process engineering or reactor design to maximize the thermal efficiency of a process. The first cat cracking process was a batch process introduced in 1915, the McAfee process, from a Lewis acid. Aluminum chloride was used in the batch reactor system. But for commercial operation, you would need a floor reactor system. So Houdry cat cracking was the first commercial continuous process introduced in 1936.
The process used the natural aluminum silica solids particles as catalysts. And in the process, we're going to look at a configuration that has three reactors in parallel. These are fixed bed reactors essentially filled with the alumina silica pellets, packed with the alumina silica palettes as catalysts. So the gas oil feed is heated in a furnace, in a fired furnace to 800 degrees Fahrenheit, and the feed is fed from the bottom of this packed bed to go through cracking on catalyst surfaces, and the products are fed to a fractionater. In the fractionater, the products are separated into gas and gasoline and LCO, light cycle oil, as the major products from cat cracking.
As the cracking goes on, the catalysts are deactivated by coke buildup. And this happens pretty fast, within 10 minutes of the introduction of the feed into the reactor. Now, since this is an endothermic reaction, you would also imagine or could visualize that the temperature will go down as the feed moves from the bottom to the top of the reactor. So cracking isn't really very homogeneous because of this decreasing temperature.
Now, once the catalysts are deactivated within 10 minutes, all coked up, you bring in steam to strip the liquids, somewhat heavier liquids that are sticking onto the catalyst surfaces to remove them into the fractionater. And some of this will end up as heavy oil. Once this operation is finished, within about five minutes, then you bring in hot air to burn off the coke to reactivate the catalyst.
But to continue this cracking process in the meantime, while you are stripping the heavier products and reactivating the customers by burning the coke, you need to switch the feed to another reactor. So that is the second in the series. So you have a continuous feed and continuous production through the system using the swing reactor configuration, as we refer to.
The same thing happens in the second reactor. The catalyst is deactivated within 10 minutes, so you bring in the steam to strip the heavier products. And while you're doing that, obviously, and then later on, burning off the coke, you should switch the feed to another reactor. That would be the third reactor in these areas. And the products are all sent to a fractionater.
So by the time the third reactor is coked up, you can now switch the feed back to the first reactor. You will have enough time to steam strip and coke or decoke the first reactor, having these additional two reactors in the series. So that's essentially the cycle in the Houdry cat cracking reaction to enable a continuous flow system while the reactors are taken out of service for decoking operations.
You see the problem here. The endothermic reaction of cracking is decoupled, really, from the exothermic reaction of burning of the coke. So for that reason, the thermal efficiency of Houdry cat cracking is not very high, and it certainly needs to be improved.
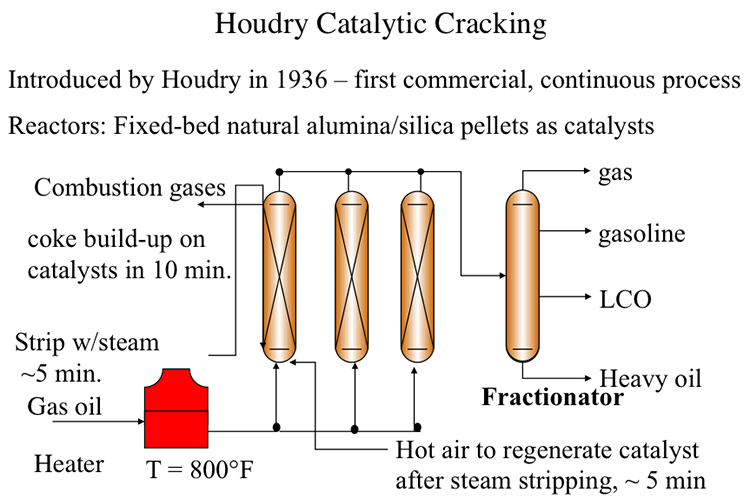
A series of swing reactors were needed to switch the feed flow from one reactor to another after approximately 10 minutes of operation. The switch to a swing reactor was necessary because of rapid coking on catalysts which, being natural materials, had a wide range of activity. Rapid coking on silica/alumina particles deactivated these catalysts and led to plugging of the reactors. After the flow was switched to another reactor, the isolated reactor was stripped with steam for five minutes to remove the liquid products adsorbed on catalyst particles. After stripping with steam, the deactivated catalysts were regenerated by burning off the coke on catalysts with hot air introduced to the reactor. Catalyst regeneration also takes approximately 5 minutes before the reactor with regenerated catalyst is ready to accept the feed again. By this time, the second reactor would be ready for the 10-minute cycle of steam stripping and catalyst regeneration. Having a third reactor in the plant would help deal with any delays/problems in reactor preparation. Considering that catalytic cracking is an endothermic process, the heat generated from burning the coke off the catalyst could be used partially to heat the catalyst particles for the endothermic reaction. A large portion of the heat in the flue gases from coke combustion was not available for the process. Therefore, the thermal efficiency of the Houdry Process was low.