
Thermafor Catalytic Cracking (TCC)
Thermafor (also referred to as “thermofor” in some sources) Cracking Process was introduced for better integration of thermochemistry (endothermic cracking and exothermic catalyst regeneration) by introducing a moving-bed configuration, rather than a fixed-bed, as shown in Figure 7.6. Catalysts used in this process were synthetic alumina/silica beads that have more homogeneous and consistent properties (e.g., activity) than the natural minerals. Catalysts particles and the feed are introduced from the top of the reactor, and the catalyst particles move downward with gravity as the cracking reactions take place on the catalyst surfaces. Steam is injected from the bottom of the reactor to carry the cracking products to the fractionator for recovery. As the particles move down the reactor, they are deactivated by coke build-up on active sites. The deactivated catalysts removed from the bottom of the reactor are sent to a regenerator unit where the coke on catalysts surfaces are burned off and the heated catalysts particles are recycled to the top of the reactors by bucket elevators. Hot catalyst particles provide most of the heat necessary for the cracking reactions in the reactor. Although the thermal efficiency of TCC is higher than that of the Houdry process, there was still a significant amount of heat loss during the transport of heated catalyst particles by bucket elevators.
Video: Thermafor (3:53)
Thermafor catalytic cracking process provided significant improvement over the Houdry cat cracking in terms of the thermal efficiency. Now, this improvement came with the change in the reactor configuration from a fixed bed in Houdry to a moving bed of catalyst now. So the catalysts are not fixed, but they are moving by gravity so that the reaction can be now conducted in just one reactor instead of having multiple reactors and switching between those reactors.
There was an improvement in the catalyst as well. Instead of using natural silica-alumina, now there are synthetic alumina-silica beads with more controlled activity, more homogeneous activity of the sites that the cracking goes on, which, of course, makes the control of the reactions better compared to the Houdry cat cracking.
So the integration of the reactor and the catalyst regenerators, as you will see, has increased the thermal efficiency very significantly over the fixed bed, the Houdry cat cracking.
Now, you can see that the feed is introduced along with the catalyst from the top of the reactors. So the particles move down with gravity at controlled flow rates along with the feed. So as the cracking goes on, on the catalyst surfaces, there is the activation. There's still coking going on, on the catalyst particles. So by the time they reach the bottom of the reactor flowing with gravity, the catalyst reactivity has been reduced to a significant extent. The catalysts are now ready to be reactivated or regenerated.
Steam, as you can see, is introduced from the bottom of the reactor to strip off all the volatile products during cracking, and the products are sent to a fractionator for separating into gas, gasoline, LCO, heavy oil, and so forth.
So the used catalysts, then, leaving the reactor is sent to a furnace where hot air is introduced to burn off the coke on the surface of the catalyst to regenerate the active sites. And the regenerated catalysts, the hot particles now, are put on bucket elevators to be sent up to the top of the reactor to close the catalyst cycles.
So the thermal integration here is such that the heat that is generated by burning the coke heats the catalyst particles. And these are hot enough to actually have the cracking take place on the surface. You can see that there is no external heater in this reactor scheme in Thermafor Cat Cracking.
But there is still more heat losses, especially in this bucket elevator system, transporting the hot catalyst particles to the top of the reactor. Thermal efficiency, although much improved over the Houdry fixed bed process, there is still a lot of room for improvement in thermal efficiency through the integration of endothermic and exothermic reactions.
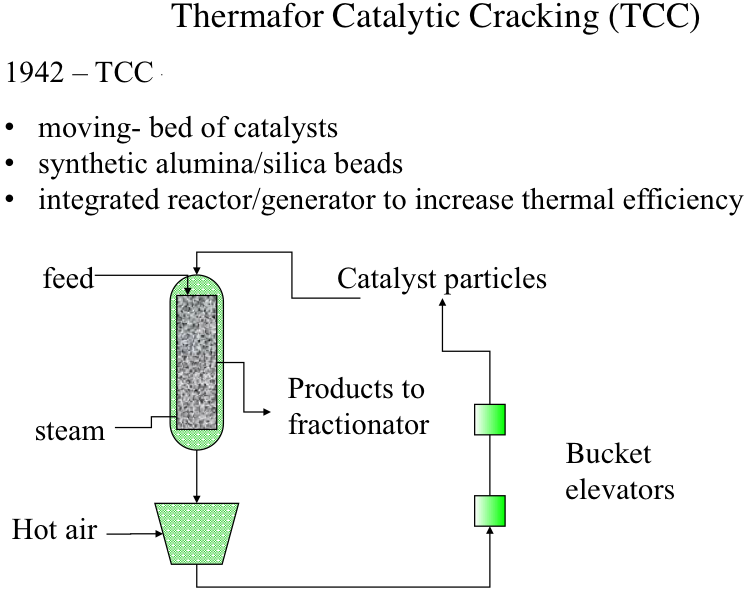