
8.1.3: Odds and Ends
There are a few odds and ends – points that need to be made, but which I haven’t discussed until now. I’ll finish out this lesson by covered these.
The shaft collar is the name given to the point where the shaft intersects the surface, and it is also a structural component of the shaft. It is typically reinforced concrete and it will be either anchored into bedrock or tied into a liner that is anchored in the bedrock. The collar serves an important structural function for equipment associated with the shaft, and it is used to limit surface drainage into the shaft.
A building or structure is associated with the shaft. If there is a hoist, there will be a headframe. Hoists are always used to haul ore up the shaft and out of the mine. The hoist may also include a cage. This is a steel structure, typically with open steel mesh construction giving it the name “cage” used to transport miners and supplies. The trip to the bottom or back up to the top is known as a mantrip. In deep mines, the cage will likely have multiple floors so that a hundred or more miners can be transported at one time. When it takes 15 to 30 minutes to make the descent, you want to minimize the number of trips! Hoists are of two general types: drum or Koepe (friction hoist). You will learn how to design both in MNG 404, and we won’t go into the differences here, although they are discussed in the text. If there is no need for a hoist, i.e., to transport ore, but only a need to transport people and supplies, then an elevator would normally be used. The elevator is similar in construction to one that you would find in a high-rise office building of 100 stories.
Here is a cross-section of a shaft showing the compartmentalization or multi-function layout. Half the shaft is dedicated to hoisting ore, and there is a skip at the bottom and a skip at the top of the shaft. As one skip is being unloaded at the top, the other is being loaded at the bottom. For reasons that will become clearer later on, this is a Koepe hoist. The other half of the shaft is dedicated to a cage. This cage is connected to a drum hoist. You might want to think about why the Koepe hoist is used in the one case and the drum hoist in the other.
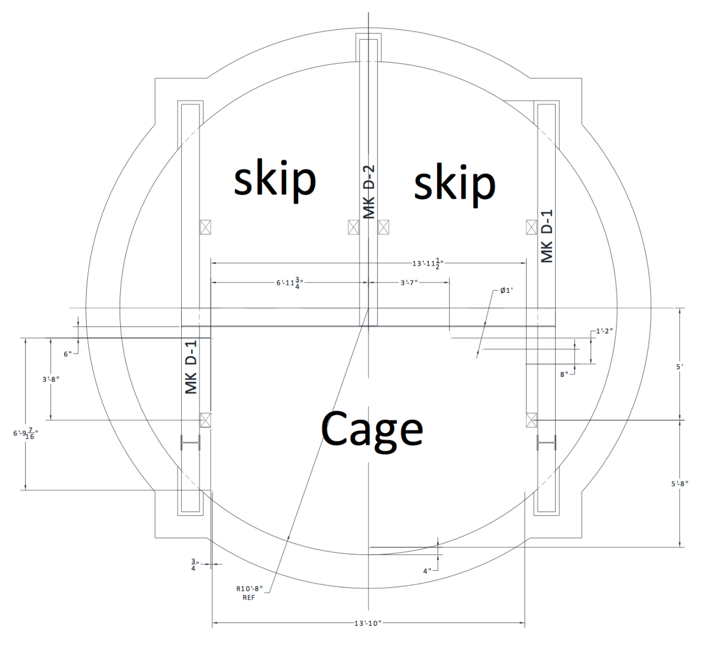
Shaft development practices have changed over the last few decades, with bored shafts being much more common and the "circular" shaft becoming all but universal for large shafts in new mines. In coal mining, about half of all shafts are now sunk by blind-boring methods. It has become common for main shafts up to 16’ to be drilled in this fashion. In addition, many coal mining companies now use bleeder shafts to simplify their longwall ventilation systems. These are sometimes drilled using blind-boring rigs. Raise-bored shafts are done as well, but access must be available underground to make this feasible, and the need for a mucking and transportation system underground makes this alternative less favorable. For large shafts, greater than 20’, in coal mines and for most metal and nonmetal mine shafts, conventional shaft-sinking methods are still commonly used.
We’ve talked little about slopes and ramps because their construction differs little from the conventional mining cycle. However, it should be noted that tunnel-boring machines are being used with increasing frequency to drive large slopes of considerable length. The cost of bringing a tunnel boring machine to a site, and setting it up is very high, and can only be justified for large diameter slopes that are greater than a few thousand feet.
The slopes used in today's coal mines are normally driven with two compartments: an upper compartment to accommodate a belt conveyor and a lower compartment containing track that is normally used for personnel and supply transport. The two compartments are separated by a horizontal concrete divider and are supported by bolts, wire mesh, or steel arches. Slopes in coal mines are often horseshoe-shaped, with widths of 17 to 20’ and heights of 13 to 14‘.
The next lesson will address the "building blocks" or basic elements of underground mines. Once we have gained access to the deposit, we are ready to begin development of the underground workings. We'll be introduced to the elements of those workings in the next lesson, and after that, we will be prepared to examine the development of underground mines for the different mining methods.
Before moving on, use these interactive activities to test your knowledge of important terms in this lesson.