
5.2.3: Electrical Systems
The power sources for mining equipment are compressed air, diesel, and electric. Most mining equipment today is powered with either diesel or electric. Diesel provides more mobility because there is no need to be tethered to an electrical cable. On the other hand, the exhaust from a diesel engine creates challenges when used in a confined space, like an underground mine, and it requires a high level of regular and sophisticated maintenance. Electric has certain inherent advantages including the ability to provide a lot of power in a small space and no toxic emissions at the machine. Large equipment, such as draglines and shovels, as well as continuous miners, is usually electric. Diesel is favored for haul trucks because of the need to be untethered.
Nearly fifty years ago, there was an effort to replace electrically powered equipment with diesel engines. Eliminating the delays associated with the tether, as well as delays associated with inevitable failures of the tethers (cables) was easy to justify; and particularly so for mobile materials handling equipment. In recent years, the air quality issues associated with diesel particulate matter and noxious gases from the engine exhaust have caused some operators to transition back to electric equipment.
I should mention battery-powered equipment, given that today we are seeing more and more battery-powered vehicles on the highways. With battery power, the tether, i.e., the cable, is eliminated, and there aren’t the drawbacks associated with diesel engines. Unfortunately, it is difficult to pack sufficient energy into a battery pack to replace the “workhorses” of hauling ore and rock. Consequently, battery-powered equipment is used for utility vehicles, such as personnel carriers or scoops for hauling supplies.
The machinery associated with production will move throughout the mine over the mine life, and as this equipment makes its way through the deposit, it will be necessary to move the electrical power system along with it. Depending on the mining method, we may need to move power every few shifts, or in other cases, only every few months. Many of you have some familiarity with power systems found in towns – the substations, power lines, and so on. Can you imagine having to move and advance such a power system on a frequent basis? In many mining methods, that is all part of a day’s work! Of course, we’ve taken steps to make it more manageable. The substations and other equipment that have to be moved are mounted on skids, crawlers, or rubber tires to facilitate movement. Couplers are used to connect and disconnect components and cables. It’s manageable!
Of course, there are other electrical loads, some of which must be moved periodically, and others that are stationary and semi-permanent. These loads would include pumps, conveyors, and illumination. Even if the mining machinery is all diesel powered, it is likely that there would be other electrical loads that must be powered. Therefore, providing electrical power will be a necessary auxiliary operation for most mining methods used in surface and underground mining.
Here is a picture of a skid-mounted power center for use in an underground mine. You can see the high voltage cable going into the box. Inside, there is a transformer to reduce the distribution voltage, typically 4.16 to 15 kV, to the level required by the machinery, typically 480 to 995 V. On the other side of this box, outside of our view, there are couplers to connect the various loads. Protective devices for each outgoing circuit are built into the power center.
Here is a picture of a similar power center, which has just been built. Here, you can get a better view of each outgoing circuit. Each cable-connected load plugs into one of these circuits. The lid of the power center is removed only for maintenance purposes.
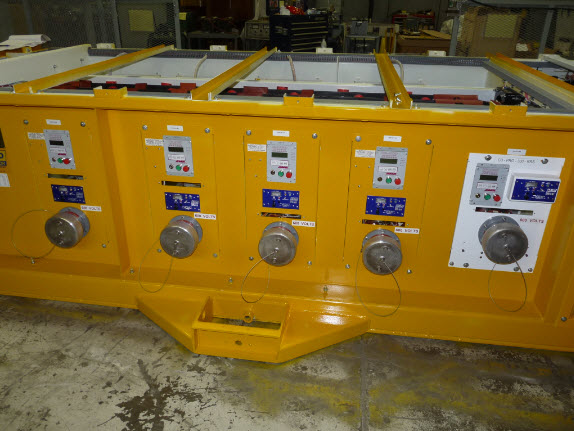
You might see a load center like the one in the following picture in a surface mine. Essentially, a shipping container has been mounted on a skid, and the required electrical components have been assembled inside the container. I’ve seen power centers in surface mines that have been built on railroad cars and old tractor-trailer beds, among others!
As I mentioned earlier, these power centers must be advanced as mining progresses. Often a “power move” will require adding additional high-voltage cable, or in some surface mines, adding additional poles and overhead lines. Some mining methods are more “electric-intensive” than others, and that also varies by commodity. Room and pillar mines in coal, salt, or trona, for example, are very power intensive, requiring significant infrastructure and frequent moves. Others, such as room and pillar mining in limestone or cut and fill mining in gold, require less electrical infrastructure and few moves. Nonetheless, providing safe, reliable, and timely power is a critical auxiliary operation in most mines.