
8.3.1b: A Practice and the Auxiliary Operation to Prevent Explosions
Fine dust that is suspended in the air can be very explosive. Coffee, coal, cotton, and flour are important examples of dusts that are explosive, and are examples of deadly explosions that do occur in industrial settings. Many processes that involve milling, grinding, and cutting, for example, can generate fine dust particles. Under the right conditions, they can fuel powerful explosions.
Fine basically means that the dust particle has a very large surface area to volume ratio. We all have practical experience with fine dust. If there is sunlight shining into your room, pick up a towel, sheet, or piece of clothing and shake it. What do you see? Dust particles floating in the air, right? Eventually, those dust particles settle onto your desk or other furniture, and then periodically you take a cloth a wipe the accumulated dust away. There are corollaries between your practical experience and the industrial issue with dusts, and we will identify them.
The dust particles that are suspended in the air, and then eventually settle are known as float dust. The exact size of the float dust is somewhat dependent on the material. For coal dust, we are interested in particles that are 75 microns or less in size. The cutting action of carbide-tipped bits, as used in continuous mining machines, and shearers, creates not only large pieces of coal, but also a range of much smaller particles. Some of these are less than 10 microns and are respirable, i.e., they are trapped in the lungs when we breathe air containing these particles. Long-term exposure to excessive concentrations of respirable dusts will lead to fatal lung diseases, e.g., black lung (coal) or brown lung (cotton). The concentration of respirable dusts is heavily regulated, and engineering controls are used to ensure that hazardous concentrations do not occur. As we’ll see, the concentration of float dust is regulated as well. The creation of these dusts is an unavoidable consequence of the cutting or processing of the materials. Therefore, if we want to avoid bad outcomes, we have to take steps to ensure that the dust does not cause harm.
Before we can mitigate the affects of float dust, we need to know a little more about the genesis of dust explosions. In general, we must satisfy three conditions to have an explosion. We need a fuel, an oxidizer, and an ignition source. In this case, the dust serves as the fuel and the oxygen in the air serves as the oxidizer. Ignition sources can be varied. A spark created when a carbide bit strikes a hard rock at the interface of the coal seam and the roof, a spark from a motor or piece of electrical equipment, or in the old days, a match used to light a cigarette. It takes a very small amount of energy to ignite a dust cloud, or for that matter, a methane-air mixture. Given this information as background, what can we do to prevent a dust explosion?
Well, we have three choices, don’t we? Eliminate the fuel, the oxidizer, and/or the energy source. We can’t eliminate the oxygen, because it is in the air that our miners are breathing. We can’t eliminate the fuel, or can we? We can eliminate the energy source, so let’s talk about that one first.
We can ban the use of smoking materials in the mine or plant. In coal mining, smoking was banned with the 1969 Coal Mine Safety Act. This eliminated many explosions in coal mines. Next, we can mandate the use of special electrical equipment. We can require that all electrical equipment used in certain areas be placed inside of explosion proof enclosures. Unfortunately, no one has devised a way to prevent frictional ignitions, i.e., when a cutting bit creates a spark when striking certain rock masses, such as quartz or pyrites. Dramatically reducing the likelihood that an energy source will exist is doable; but guaranteeing that there will never be an energy source is not. Therefore, we have no choice but to try to eliminate the fuel source. While it is impossible to complexly eliminate the fuel source, we can dramatically reduce the chance of satisfying the three concurrent conditions necessary for an explosion, if we dramatically lower the likelihood of two of the conditions.
We cannot stop the generation of float dust, although researchers are attempting to devise ways to control it at the source. We can take two important steps after it has been created. Before talking about those steps, let’s first look at the anatomy of a dust explosion; and I need to preface that discussion with this fact: dust explosions follow from a methane explosion. We will use that as our starting point.
- A small volume of methane is ignited, perhaps by a frictional ignition. 99.999% of the time, our properly engineered and operated ventilation system is diluting the gas as it is liberated during cutting, and the ignition amounts to no more than a “little pop and flash of light.” If there is a little more methane present, the initial ignition will grow in size. High temperatures are produced and the gas and surrounding air will rapidly expand. The force of this explosion and the attendant damage will depend on the volume of methane present. We take significant steps to prevent the presence of an explosive mixture of methane and air, but sometimes multiple people fail to perform their responsibilities, and the unthinkable happens.
- The rapidly expanding gases create a shock wave, which produces a wind out in front of the fireball. The fireball will dissipate as soon as the methane is consumed, and the damage could be confined to a relatively small area; unless another fuel source is present. Any guesses on the other fuel source? Yes, accumulations of float dust.
- The traveling shock wave “stirs up” and dissipates accumulated float dust. A moment later, the fireball comes through and ignites this dust cloud, producing a violent explosion. At this point, the explosion may transition from a deflagration to a detonation. When it detonates, the shock wave will be moving faster than the speed of sound! The propagation of the explosion at this point does not require any methane – only dust. The moving explosion will entrain float dust and essentially at that point, it is carrying its own fuel! Even if it reaches a point where there is no float dust, there will be sufficient fuel entrained to allow propagation over a considerable distance. And, of course, if additional dust is encountered, the explosion will continue that much further. The amount of energy involved, as you might imagine, is staggering. A dust explosion can travel over miles and miles of entries, leaving nothing but twisted metal and charred remains in its path.
If you were standing downstream of a mine explosion, you would see the flame front approaching at a speed in excess of 1200 ft./sec. You can see the effect of the shock wave out in front of the flame front.
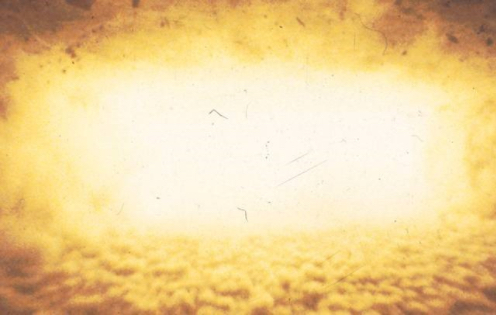
Often, these explosions will ultimately vent to the outside. Here is one such event – a research experiment, not an operating mine explosion, at the U.S. Bureau of Mines’ experimental mine near Pittsburgh. Much of what is known about these explosions and their prevention was developed by researchers at this facility.
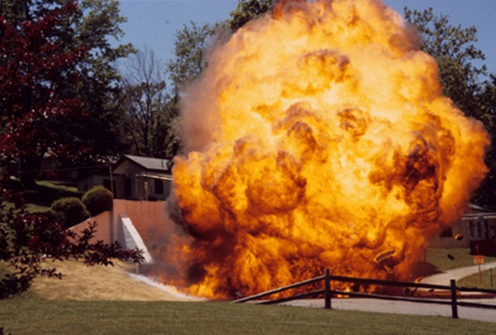
Fortunately, these explosions are rare in the U.S. The last coal dust explosion occurred in 2010. You have to go back four decades to find the one before that (actually there were a few smaller gas explosions during that period as well). Unfortunately, they have not been eliminated.
So, what more can we do to prevent these horrible events? Hopefully, this more detailed explanation of explosions has given you an idea or two! What do you think?
First off, we need to clean up accumulations of float dust. In fact, the law requires such cleanup to occur, and you will be fined if an inspector finds excessive accumulation of float dust. This is a very important “housekeeping” function. While you can successfully cleanup float dust accumulations near belt drives and along the belt line, it is impossible to prevent fine layers of dust from accumulated on the mine ribs and floor. Consequently, we need another approach, and that is the application of rock dust, which is known as rock dusting. We apply rock dust with rock dusters. I admit these terms are not very imaginative, but at least they will be easy to remember!
What is this rock dust and why is it effective? Rock dust is usually limestone that has been crushed to a fine powder. When we rock dust, we are applying, and literally blowing, this powder onto every surface in the coal mine. What purpose does this serve? Well, first off, this dust is inert, i.e., it is not combustible. Let’s assume that we’ve applied rock dust to all surfaces, and with this practice in place, let’s revisit the propagation of the explosion.
As explained previously, the shock wave moving ahead of the flame front disperses any dust into the air, and then the flame front ignites the dispersed dust cloud, and the explosion continues to propagate. But, what if the dispersed dust were an inert material like rock dust? Two good things would happen. First, the explosion would be deprived of new fuel, and second, the mass of the rock dust will reduce the temperature of the flame front. The net effect is that the explosion is quenched. Thus rock dusting can prevent dust explosions; but only if it is applied in sufficient quantity. Based on NIOSH research, MSHA regulations require that sufficient rock dust be applied so that the resulting mix of float dust and rock dust contains a minimum of 80% of inert, i.e., incombustible, content. Rock dusting is an essential and critical auxiliary operation in coal mining, and the law requires that all areas within 40’ of the active mining face be rock dusted.
You may be interested to know that you cannot use just any rock dust for this purpose. The law defines the specification for rock dust as follows:
Pulverized limestone, dolomite, gypsum, anhydrite, shale, adobe, or other inert material, preferably light colored, 100 percent of which will pass through a sieve having 20 meshes per linear inch and 70 percent or more of which will pass through a sieve having 200 meshes per linear inch; the particles of which when wetted and dried will not cohere to form a cake which will not be dispersed into separate particles by a light blast of air; and which does not contain more than 5 percent combustible matter or more than a total of 4 percent free and combined silica (SiO2), or, where the Secretary finds that such silica concentrations are not available, which does not contain more than 5 percent of free and combined silica.
I am not going to test you on the specific details of this definition, but I thought that you might be interested to know the standard.
Rock dusters come in a variety of shapes and sizes, but consist of a storage vessel for the bulk rock dust, a feeder, and a compressed air system to entrain the rock dust in an air stream. Application can be through hoses directed by a miner or broadcast in all directions around the rock duster. In some instances, it is desirable to apply rock dust continuously, and in those cases, trickle dusters dispense a small but continuous stream of rock dust into the air stream. This is done, for example, in certain return aircourses and belt entries.
One of the most surprising sights to people going into a coal mine for the first time is that the mine is white rather than black! Rock dusting is the reason for that!
It’s tough to find a really good video illustrating rock dusting. This one here (2:53) does a reasonably good job at the 2-minute mark; and the other operations that you can see in this clip are worthwhile watching as well.
Ok, let’s continue with our study of unsupported mining methods!