
Efficiency Stagnation
Perception of Diminishing Financial Returns in Sustainability Projects
The advent of Lean/Six Sigma adoption in organizations worldwide has also brought with it requisite continuous improvement efforts that analyze virtually every important process and material on a priority-weighted basis. In some cases, the organization undertakes intensive exercises to unearth inefficient processes, then the group elects to engage on the improvement of a handful of those processes by creating task forces. What this has meant for many organizations is that the most inefficient or wasteful areas of the business were likely identified years ago, have received one or more cycles of continuous improvement efforts, and perhaps even the efforts of outside consultants or experts.
This leaves many organizations today in a situation where the cost and effort to take on the next level of new efficiency projects can't be justified by financial measures alone, or cases where the waste is so small as to be inconsequential. In these projects, it isn't even necessarily that the capital needed is an issue, but it tends to be more of a problem of lacking return on investment and overly long payback periods. Many organizations have found themselves in a place where the progress of these higher-level tiers of efficiency projects become dependent on larger trends over time, which may include factors such as:
- Change in fuel or energy costs (i.e., lighting and machine upgrades become more cost effective, or alternatively, less expensive freight opens waste-to-energy as an option)
- Increased material costs (i.e., increased cost of wasted materials)
- Increased cost of disposal (i.e., waste material becomes prohibitively expensive to treat or landfill)
- Change in regulations (i.e., increased regulation requires a different approach, or alternatively, loosened regulations open options before prohibited)
- Significant changes in technology
- New business entries (i.e., a waste-to-energy site opens 30 miles away, making transportation viable)
- et cetera
What we may therefore see is a period of "efficiency stagnation," where the organization may have new efficiency projects queued based on earlier identification, exploration, and scoping (i.e., continuous improvement efforts), but is waiting for something to change to make those programs viable. Unfortunately, those changes don't always work in favor of progressing efficiency, as we have seen some of the same free market forces and commodity prices which helped establish widespread industrial recycling, for example, regress as supply increases. Essentially, recycling's own popularity in industry has made it more difficult for recycling companies to profit, in some cases.
The below is a summary image from a bit of research I did with 304 facilities in the US in 2013, exploring the state of waste minimization. Note the 40+ point drop in adoption rates for the more established "classic" forms of recycling/waste reduction projects to some of the "next level" projects.
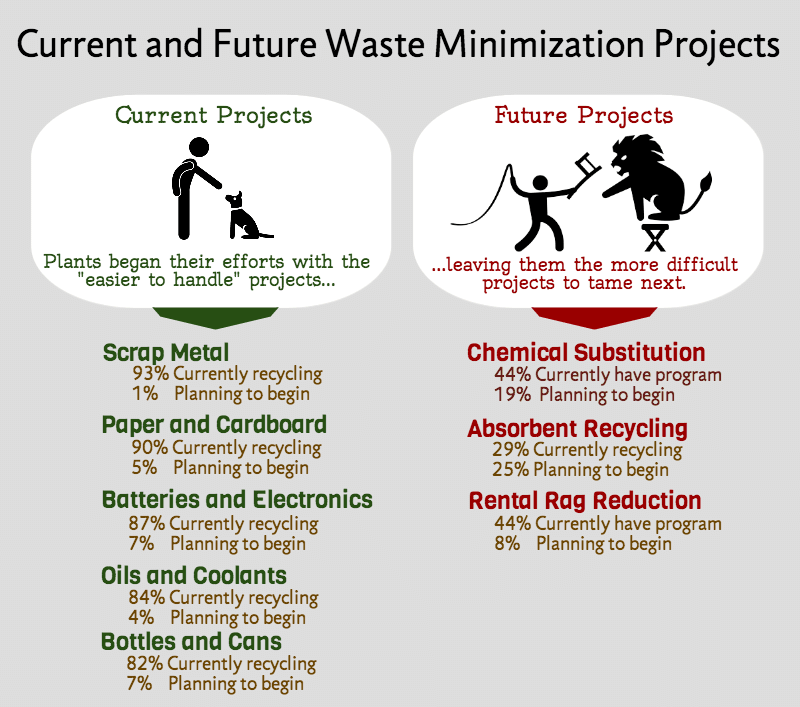
An Opportunity for Innovation
What is important for us to note is that this potential stagnation in efficiency projects is not due to a lack of interest on the part of organizations, nor is it due to a lack of capital. Needless to say, an engaged organization with money to spend makes for a fertile ground for opportunity and innovation.
And while we may think that those larger trends cited earlier are the only external tailwinds that can spur an organization to pull an efficiency project from the queue, we must consider an opportunity in the information itself: The fact that these projects are contingent on some external change also signals they are contingent on an organization 1) knowing an external change has happened and, 2) having at least a passing understanding of the interactions between different factors.
Organizations are, by nature, resource constrained. Even the most sustainability- and efficiency-minded organization does not have time to continuously check the state of the art of every process, material, and resource under their purview. So, while a project may have been placed in a queue, it may not be because of the actual state of the situation, but simply the organization's perception of the situation at a given point in time. They may have had limited information on new options or processes, they may have had an incomplete understanding of the situation itself, there may have even been conflict of interest issues in displacing existing vendors or suppliers. Nonetheless, the issue with getting these efficiency projects out of the queue and into action may be as much about quality of information as it is about the actual project to be enacted itself.
Allow me to illustrate:
A few years ago, in talking to plant managers, I started seeing a bit of a trend. When discussing their waste minimization programs and what projects to take on, the discussion always revolved around pounds or tons of waste, but very, very rarely around density. The conversation would go something like this:
Me: "So what's next for your waste minimization program? Have anything on the radar?"
Plant Manager: "Well, we were looking at recycling waste X, but based on our tonnage to the landfill, it looks like it would cost us 10% more to have it recycled."
Me: "What kind of density is it and do you know what you're paying in dumpster rental?"
Plant Manager: (pause) "All I know is that we are paying $90/ton for tonnage, and I haven't dug any deeper because the recycling was more expensive."
It was prevalent enough of a problem I created an Excel-based tool which would allow someone to input ALL of the data related to landfilling a waste, including dumpster rental, tonnage, pull fees, and density (either extrapolated or pulling from EPA-accepted densities of 100 industrial wastes) to understand the full cost of disposal, by prorating all costs by either weight or density. So, if a dumpster was filled with something fluffy, like Styrofoam peanuts, the tonnage would be very inexpensive, but it would be burdened with the full cost of dumpster rental, etc, (which, incidentally, could easily cost twice as much as tonnage). In the case of a heavy material, like brick, it would bear the appropriate costs of tonnage, but only a prorated portion of dumpster rental. It would allow the same calculations for recycling the material, including the cost of any necessary machinery or additional labor.
In the end, it would also calculate payback periods and create an executive summary, as well as calculating cost benefit of source reduction of a waste.
So, only after seeing the full picture, could a facility make the right decision. And in many cases, accounting for the full, real financial burden of landfilling ended up swaying cases heavily toward recycling options. In one example, a recycling program savings had been accounted at $26,000 a year using flawed calculations... with the calculator, those actual savings were shown to be closer to $110,000. In fact, in some test cases, neglecting density could skew actual cost to dispose of some materials by nearly 300%.
In two years, more than 3,000 facilities worldwide of all sizes would use this tool to evaluate the actual costs of landfilling v. recycling to get programs 'out of the queue.'
Why do I mention this?
Because a flawed understanding of just one fundamental portion of the efficiency equation has the ability to keep countless programs on the shelf... and, by bringing new information or insight to the table, those programs can be moved forward in a meaningful way.