
The main well consideration is the anticipated production rate from the reservoir. As we saw in the previous lesson, the pressure drop for a given tubing size is directly related to the production rate (or rates for multi-phase flow). For a naturally flowing well, the reservoir pressure must be great enough to lift the reservoir fluids up the well and deliver these fluids to the surface facilities. Therefore, the producing rate needs to be considered in the sizing of the tubing.
For the same reasons, the current and future reservoir pressures must also be considered in the well design. It is this pressure that drives the fluids to the production facilities. If the pressure has dropped too low due to fluid production, then artificial lift (gas lift or pumps) may be required.
The geology of the reservoir is also of vital importance in the well design. As we will see, reservoirs consisting of a single zone (or reservoir layer) may have one type of completion, while reservoirs comprised of multiple zones may require more complex completions. Typically, we would like to be able to isolate individual zones (or groups of zones) at some future point in time if required. This would occur if the reservoir conditions in some zones change at a different rate than in other zones. For example, if a well is originally producing at a low watercut, , and at some future date, one layer begins to produce water at a higher watercut than the other reservoir layers, then, we would want to be able to isolate this high watercut zone (to shut it in), while continuing to produce from the low watercut zones. We will see that some well completions will allow us to provide this ability for zonal isolation, while others will not.
In addition, as mentioned earlier, if the reservoir rock is comprised of unconsolidated rock or rock susceptible to fines migration, then we will need to design wells and completions that allow for sand control. If sand or fines enter the well, they will settle at the bottom of the well and may eventually result in Sand Fill: sand or rock material accumulating in the well and covering some or all of the well perforations.
Also, if the reservoir rock is low permeability, then we may need to consider stimulating the well in our original completion design. This how we produce gas in unconventional gas wells, such as Marcellus Shale wells in Western Pennsylvania. Figure 7.01 illustrates a typical well completion for a Marcellus Shale well.
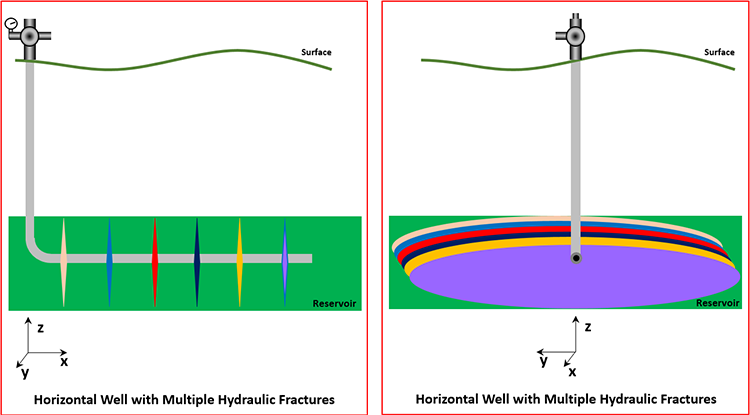
In this completion design, a long horizontal well is stimulated with multiple hydraulic fractures. The need for this type of completion is because of the ultra-low permeabilities in shale reservoirs. Shale permeabilities, including the Marcellus Shale, range from nano-Darcies (10-9 Darcies) to micro-Darcies (10-6 Darcies). These orders of magnitude are in contrast to the milli-Darcies, md, (10-3 Darcies) that we typically deal with in the oil and gas industry. The reason that the Marcellus Shale has opened up in the last two decades is because of completions like that shown in Figure 7.01 and the technologies behind these completions.
In addition, deep wells will inevitably encounter high pressures and temperatures and often encounter high concentrations of Acid (Corrosive) Gases, hydrogen-sulfide, H2S, and carbon-dioxide, CO2. In addition to being a very corrosive gas, H2S, is highly toxic. The high pressures and temperatures require all downhole equipment be certified for those conditions. All well tubulars in highly corrosive environments require special CRA (Corrosive Resistant Alloys) steel.
In earlier lessons, we discussed the drive mechanisms in oil reservoirs. These drive mechanisms may have some significance in the types of well completions used in the reservoir. The natural drive mechanisms for oil reservoirs encountered during Primary Production (the first stage of oil production) are:
- rock and fluid expansion
- solution gas drive
- gas cap drive
- gravity drainage
- natural aquifer drive (or water encroachment)
From this list, two of the drive mechanisms, solution gas drive and gas cap drive, are drive mechanisms that are due to the presence of a free gas phase. If this free gas results in high producing GORs, then the well completion must be capable of handling this gas or capable of isolating the reservoir zones containing the free gas. Likewise, the natural aquifer drive may result in mobile water in the reservoir and excessive water production with high watercuts. Again, the well completion must be designed to be able to isolate this water production.
During Secondary Production (a second stage of oil production), we may inject gas or water into the reservoir to displace oil towards the production wells. In these cases, we will need totally different well designs for our injection wells than we would use for our production wells. In addition, since we are adding these external fluids into the reservoir, we must plan our production wells to eventually produce some of these fluids. For example, if we are injecting water, even if our original well and completion design allows for zonal isolation, we will eventually start producing this water. As we saw in Lesson 6, the presence of water in the produced fluids will result in a heavier well stream, and we may need to consider artificial lift (gas lift or pump) for our production wells. As a second example, if we inject steam to improve recovery of high viscosity oils, then all of our downhole equipment must be certified for production at these elevated reservoir temperatures.
As we can see, there are many possible situations that can be encountered by a single well and infinitely more combinations of these situations. Therefore, there is no “cookbook” for well design. The best advice that I can give is to let the nature of the problem dictate the nature of solution. We can go over several common situations and example completion and well designs used in these situations.
In this lesson, we will discuss the following aspects of well design:
- well orientation
- completion design
- tubing size
- artificial lift
- well stimulation