
Bernoulli’s Equation
Bernoulli’s Equation forms the basis of the steady-state tubing performance. Bernoulli’s Equation is simply an energy balance on a given system. In our case, that system is the production tubing. Bernoulli’s Equation can be written as:
In this equation, all of the terms have the units of lbf-ft. The variables in this equation are:
- U1 and U2 are the Internal Energies stored in the fluid at two points in the system, lbf-ft. This internal energy is energy at the molecular level and cannot be measured in an absolute sense. We can establish the relative change in the internal energy (ΔU=U1−U2) by assigning a zero value at some specific set conditions.
- p1 and p2 are the pressures at two points in the system, psi
- V1 and V2 are the volumes of the fluid at two points in the system, ft3
- The terms p1V1144 and p2V2144 are the Energies of Expansion or Compression, lbf-ft. These terms represent compressional energy stored in the fluid (similar to the energy stored in a compressed spring).
- m is the mass of the fluid in the system, lbm
- v1 and v2 are the velocities of the fluid at two points in the system, ft/sec
- gc is the Universal Gravitational Constant, 32.174 lbm-ft/lbf-sec2
- The terms mv212gc and mv222gc are the Kinetic Energy of the fluid in the system, lbf-ft
- g is the Local Acceleration due to gravity, ft/sec2. The local acceleration due to gravity varies from location to location but is approximately equal to 32.174 ft/sec2. The ratio of ggc is approximately equal to 1.0 lbf/lbm.
- z1 and z2 are elevations above some reference point, typically sea level, ft
- The terms mgz1gc and mgz2gc are the Potential Energies of the fluid at two points in the system, lbf-ft
- QH is the Thermal Energy added to or removed from the system, lbf-ft. In Equation 6.01, QH is positive if thermal energy is added to the system or negative if thermal energy is removed from the system (note: 1 BTU = 778.169 lbf-ft)
- W is the work added to or performed by the fluid, lbf-ft. In Equation 6.01, QH is positive if work is added to the system (for example, with a pump) or negative if work is removed from the system (for example, by turning a turbine)
There are many engineering Thermodynamics concepts in this equation which are out-of-scope for this course; however, we can illustrate the application of Bernoulli’s Equation in the context of flow through tubing with Figure 6.04.
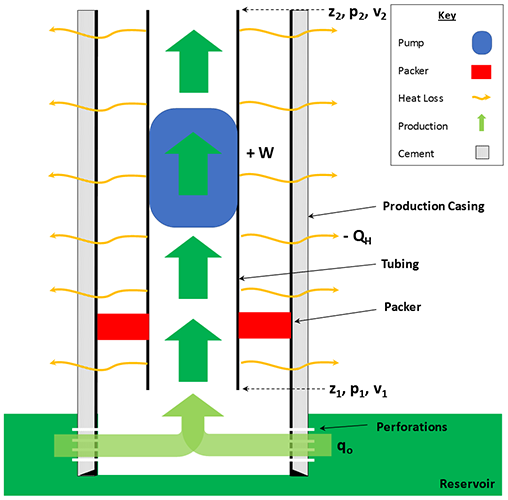
In Figure 6.04, we have a length of vertical tubing defined from a depth of z1 to a depth of z2 with an inner diameter of DID. A mass of oil enters the tubing at z1 at a volumetric rate of q (ft3/sec) at a pressure of p1 and a velocity of v1=qA 4qπD2ID. As the oil travels up from the reservoir, the surrounding rock is cooler than the oil due to the local geothermal gradient, and heat is lost (−QH) from the hot oil to the surrounding cooler rock. Flowing upward, the oil encounters a downhole pump which supplies work (+W) to the system. The oil finally reaches point z2 in the tubing with a Terminal Pressure of p2 and Terminal Velocity of v2.
Without going into the thermodynamic details, Equation 6.01 can be rewritten in differential form as:
Where:
and,
- p is the pressure at a point in the tubing, psi
- l is the distance along the axis of the tubing, ft
- 144 is a unit conversion constant, in2/ft2
- 12 is a unit conversion constant, in/ft
- gc is the Universal Gravitational Constant, 32.174 lbm-ft/lbf-sec2
- g is the Local Acceleration due to gravity, ft/sec2. The local acceleration due to gravity varies from location to location but is approximately 32.174 ft/sec2. The ratio of ggc is approximately 1.0 lbf/lbm
- θ is the angle of inclination above the horizontal, dimensionless
- fDW is the Darcy-Weisbach Friction Factor, dimensionless
- v is the velocity of the fluid at the point in the tubing, ft/sec
- ρ is the density of the fluid, lbm/ft3
- DID is the Inner Diameter (ID) of the tubing, in
- z is the elevation of the point in the tubing above a reference point, typically sea level, ft
The units of each of the terms in Equation 6.02 and Equation 6.03 are psi/ft. The well orientation for Equation 6.02 and Equation 6.03 is shown in Figure 6.05.
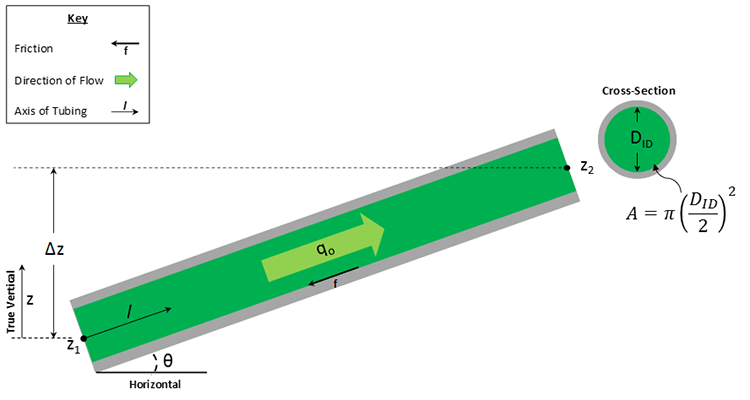
In Equation 6.02, I have neglected the Heat Transfer, QH, and Work, W, terms. If we have significant heat transfer or a device that adds or performs work, we can include these terms into the equation.
Expanding on the terms in Equation 6.02, the elevation term, (dpdl)Elevation, is simply the change in the potential energy as the fluid flows through the tubing in the direction of l. Note that in the convention shown in Figure 6.05 with the z-direction upward, point z2 has a higher potential energy than point z1 because it has a higher elevation. The friction term, (dpdl)Friction, is the irreversible loss of energy due to friction as the fluid flows past the stationary tubing wall. Friction always acts in the direction of opposite of flow. For single-phase flow, the only friction component occurs at the liquid-tubing interface. In multi-phase flow where phases are flowing at different velocities, there will be a friction component occurring at the phase boundaries also. Finally, the acceleration term, (dpdl)Acceleration, is the change in energy resulting from the acceleration or deceleration of the fluid going around bends in the tubing. The acceleration term is often neglected in tubing calculations.
As mentioned earlier, the friction factor, fDW, in Equation 6.03b is the Darcy-Weisbach friction factor. This equation is co-credited to Henry Darcy, who is the same Darcy that gave us Darcy’s Law. The Darcy-Weisbach friction factor is the ratio of the shear stress at the wall and the kinetic energy of the fluid on a unit volume basis. This friction factor was plotted by Moody[1]as a function of the Reynolds Number[2],[3], Re, and the Relative Roughness (εDID). The Moody Diagram is shown in Figure 6.06.
Note, we will be using the Darcy-Weisbach friction factor, fDW, which is not to be confused with the Fanning Friction Factor, fF[4]. The Fanning friction factor is ¼ the value of the Darcy-Weisbach friction factor, that is: fF=14fDW. The difference between the two friction factors is that the Darcy-Weisbach friction factor is typically used for closed circular pipes, and uses DID as the diameter, while the Fanning friction factor can be used for open conduits and uses the concept of the “hydraulic radius” as a measure of the diameter: rh=Ap. Where rh is the hydraulic radius, A is the cross-sectional area of flow (length squared), and P is the “wetted perimeter” (length). The wetted perimeter is the perimeter of the cross-section in contact with the conduit (portion of the cross-section that is “wetted” by the fluid).
The Reynolds Number, Re, is a dimensionless group that represents the ratio of the inertial forces to the viscous forces within the fluid and is used to characterize laminar and turbulent flow regimes. For our application of flow through pipe, the Reynolds Number is defined by:
Where:
- NRE is the Reynolds Number, dimensionless
- 1488.0 is a unit conversion constant, ft-sec-cp/lbm
- 12 is a unit conversion constant, in/ft
- 124 in an equation constant
- DID is the Inner Diameter (ID ) of the tubing, in
- v is the velocity of the fluid in the tubing, ft/sec
- ρ is the density of the fluid, lbm/ft3
- μ is the dynamic viscosity of the fluid, cp
Note, Equation 6.04a can be expressed in an equivalent form in terms of flow rate, q(bbl/day):
Where the velocity term was replaced with the rate term: v(ftsec)=qA=(4)144(in2ft2)πD2ID(in2) 5.615(ft3bbl) q(bblday)24(hrday)60(minhr)60(secmin).
At lower values of Re (Re<2,000) flow is in the laminar flow regime, while at higher values of Re (Re>4,000) flow is in the turbulent flow regime. As we see in the Moody Diagram, Figure 6.06, in the turbulent flow regime the friction factor is a function of the Reynolds Number and relative roughness of the pipe (εDID). The relative roughness is a dimensionless quantity that is defined as the length of protrusions (lumps, pipe defects and imperfections, pits from corrosion, etc.) divided by the inner diameter of the tubing. It is a measure of the departure of an actual steel pipe from an idealized, smooth pipe. Figure 6.07 illustrates the concepts of absolute and relative roughness, while Table 6.03 shows typical values of the absolute roughness, ε, for different materials.
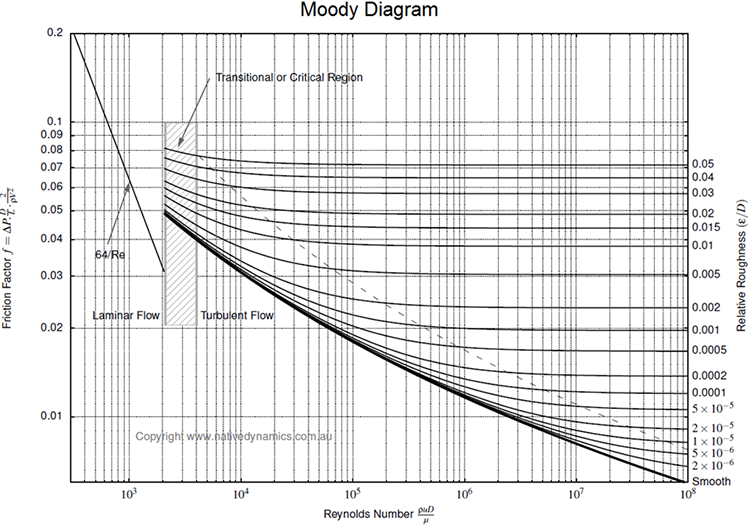
In the laminar flow regime (Re<2,000), the Darcy-Weisbach friction factor is a function of the Reynolds Number only and can be determined by:
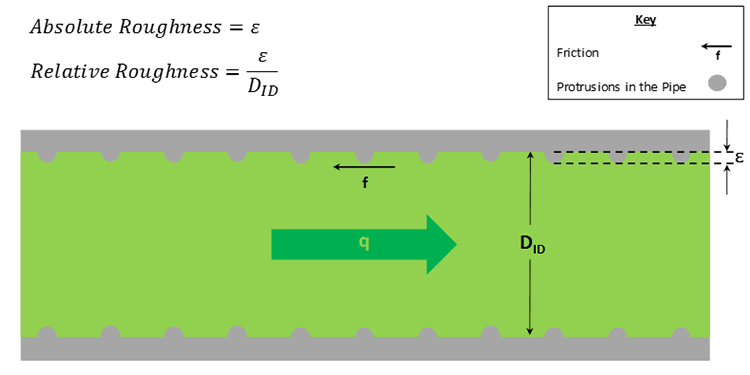
Material | ε (mm) | ε (in) |
---|---|---|
Idealized smooth surface – any material | 0.0 | 0.0 |
Concrete – coarse | 0.2500 | 0.009842 |
Concrete – new smooth | 0.0250 | 0.000984 |
Drawn tubing | 0.0025 | 0.000098 |
Glass, Plastic Perspex | 0.0025 | 0.000098 |
Iron – cast | 0.1500 | 0.005906 |
Sewers – old | 3.0000 | 0.118110 |
Steel – mortar lined | 0.1000 | 0.003937 |
Steel – rusted | 0.5000 | 0.019685 |
Steel – structural or forged | 0.2500 | 0.009842 |
Water mains – old | 1.0000 | 0.039370 |
As previously discussed, in the turbulent flow regime, the Darcy-Weisbach friction factor is a function of both the Reynolds Number and the relative roughness. To calculate the friction factor in the turbulent regime, the Implicit Colebrook Equation[6] can be used:
We say that this equation is implicit because the friction factor, fDW, appears on both sides of the equals sign. Therefore, to solve this equation, we must iterate on a solution. That is, we make an initial guess at fDW and use it on the right-hand side of the equation to calculate a new fDW on the left-hand side of the equation. We repeat this process until the two values of fDW (the recently calculated value on the left-hand side of the equation and the value used in the calculation on the right-hand side of the equation) are sufficiently close. To start the process, an Explicit Formula for fDW, such as the Swamee-Jain Equation[7], is used:
We say that Equation 6.07 is an explicit formula because the friction factor does nor appear on the right-hand side of the equation, and we can solve for it explicitly. The Swamee-Jain Equation[7] is an approximation to the Colebrook Equation[6] and can also be used directly in calculations.
[1] Moody, L. F. (1944), "Friction factors for pipe flow", Transactions of the ASME, 66 (8): 671–684
[2] Stokes, George (1851). "On the Effect of the Internal Friction of Fluids on the Motion of Pendulums". Transactions of the Cambridge Philosophical Society. 9: 8–106.
[3] Reynolds, Osborne (1883). "An experimental investigation of the circumstances which determine whether the motion of water shall be direct or sinuous, and of the law of resistance in parallel channels". Philosophical Transactions of the Royal Society. 174 (0): 935–982.
[4] Fanning, J. T. (1877). A practical treatise on water-supply engineering, Van Nostrand, New York, 619
[6] Colebrook, C. F. (1938–1939). "Turbulent Flow in Pipes, With Particular Reference to the Transition Region Between the Smooth and Rough Pipe Laws". Journal of the Institution of Civil Engineers. London, England. 11: 133–156.
[7] Swamee, P.K., and Jain, A.K. (1976). Explicit equations for pipe flow problems. J. Hydraul. Div. ASCE 102 (HY5), 657–664.